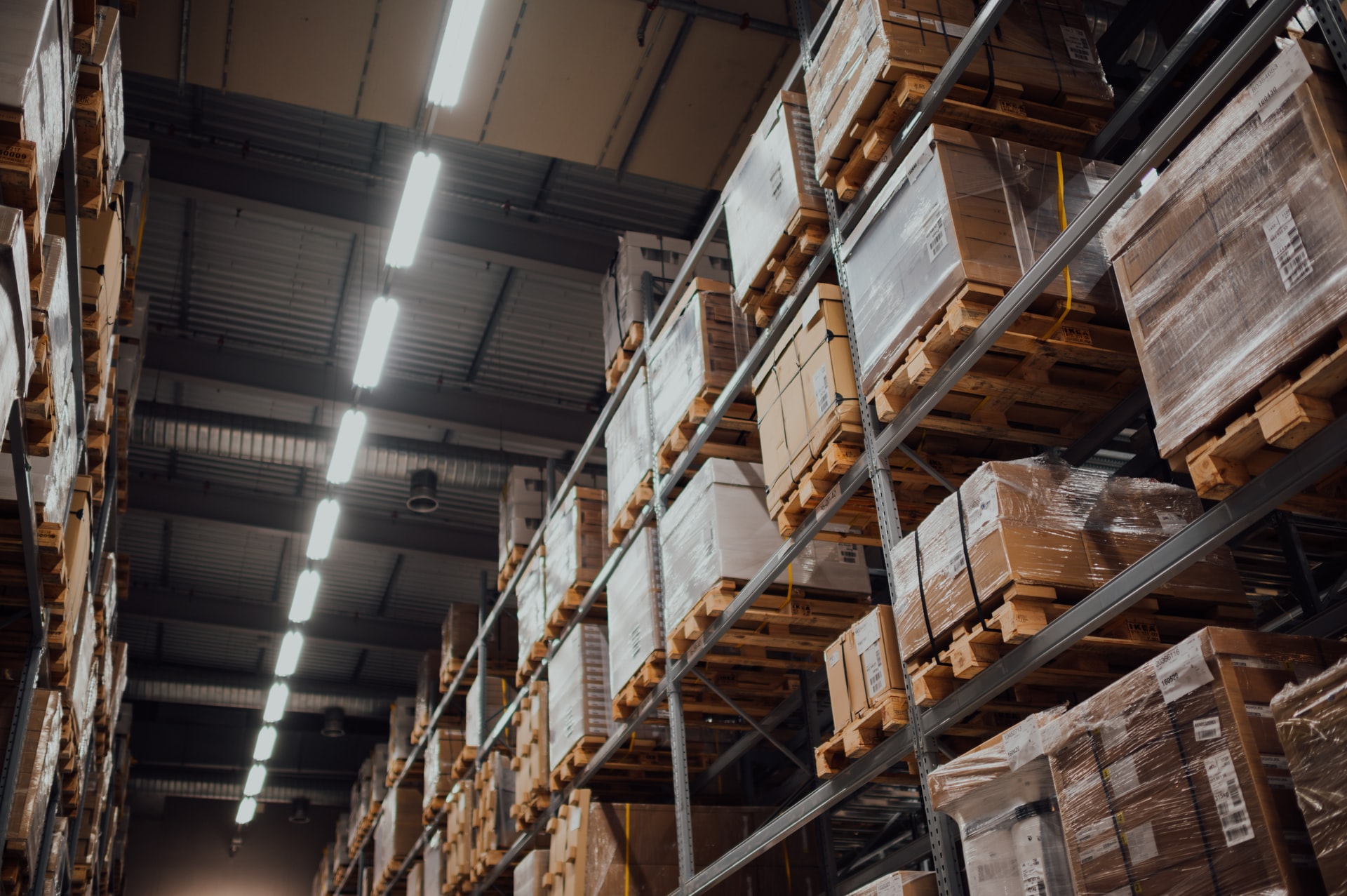
2021 Warehouse Automation Trends You Need to Know
March 16, 2021 - Revolutionized Team
Revolutionized is reader-supported. When you buy through links on our site, we may earn an affiliate commission. Learn more here.
Major trends in the logistics and shipping industry — including the rise of Industry 4.0 tech and the impact of the COVID-19 crisis — are pushing warehouse owners to invest more and more in warehouse automation.
New technology, like self-piloting robots and advanced warehouse management solutions, has made warehouse automation more practical than ever. The growth of specialized IIoT solutions has also made it much easier for warehouse owners to gather the data needed for warehouse automation.
These are some of the trends that will likely define warehouse automation in 2021 and potentially through the rest of the decade.
Familiarity with these trends will be essential for any business interested in investing in warehouse automation.
1. IoT Data Collection
The growing availability of industrial IoT sensors and other data-capturing technologies means warehouse owners are now capable of gathering more information than ever on warehouse operations and workflows.
In practice, this has enabled warehouse owners to both make better decisions about warehouse management and enable new, highly automated warehouse management systems.
For example, smart lighting systems can automatically adjust internet-connected warehouse lights throughout the day, optimizing for visibility and energy efficiency as natural light waxes or wanes. Smart HVAC systems can be similarly programmed for an automatic response, making slight adjustments to temperature as needed to balance worker comfort with resource savings.
For businesses to provide a comfortable working environment and reduce unnecessary resources, these smart systems are a major asset.
The same technology may also allow warehouse managers to track individual pallets or pieces of equipment. With the right combination of sensors, they can build a real-time, bird’s-eye view of their warehouse that can enable more complex automated solutions.
2. Big Data and Predictive Analytics
At scale, however, it may not be possible to process data at the volume gathered by these IoT sensors. New tools, like big data analytics software or AI-powered analytics tools, can help warehouse managers process this data and enable predictive analytics — the use of data to build more accurate forecasts about future events.
Predictive analytics will enable a range of new management strategies — like predictive maintenance, which is an alternative to (or upgrade for) scheduled maintenance.
With a predictive maintenance strategy, owners outfit key warehouse equipment with sensitive IoT sensors. These sensors track operational data related to the equipment’s performance — like device timing, vibration, or temperature.
After establishing a baseline of standard performance, the sensors can watch out for unusual variations in equipment performance — like off timing or extreme vibrations — that can signal the potential for failure.
These systems can then give supervisors a heads-up on potential performance issues, allowing them to avoid damage or unusual operation that may lead to injury or costly downtime.
Advanced systems that have direct control over equipment may even be able to automatically stop machines on the verge of failure, potentially minimizing damage and injuries, and helping to cut down on the overall cost of repairs.
This approach can also help managers cut down on unnecessary equipment check-ups — both saving money and protecting sensitive equipment from damage that can occur during those check-ups.
Similar approaches can help enable new algorithmic warehouse management strategies.
With enough data, it’s possible to find a range of inefficiencies that can be smoothed out — or potential areas where workflow adjustments may help boost efficiency or prevent injuries.
Importantly, data collected by IoT sensors will be available to remote management staff — meaning that, even during COVID-19, when it’s not possible for all team members to be on-site, workers still have access to the indicators of equipment health and warehouse productivity that these systems automatically produce.
3. Blockchain for Warehouse Automation and Traceability
Despite major losses in the overall blockchain market between 2018 and 2020, use of the blockchain in the industrial world has grown steadily over the past few years.
In the warehouse and logistics sectors, business owners are finding new ways to use the blockchain — a kind of distributed, digital ledger technology best known for powering cryptocurrencies like Bitcoin.
In the industry and the supply chain at large, the technology may help improve traceability and build trust between parties.
The tech can also provide real-time updates to all stakeholders involved in shipping goods, including warehouse owners. With the blockchain, warehouse owners may be able to receive advanced notice on when to expect a shipment, helping them arrange for storage or processing.
Warehouses that work closely with farms or food and beverage manufacturers are likely to be some of the biggest beneficiaries of the technology. With blockchain, it’s possible to automatically generate a trustworthy record of origin and transportation for every piece of produce that originates from a given farm or ranch — then update that record as that produce moves through the supply chain.
This information can help warehouses better manage food storage by automatically prioritizing older food items for shipping, potentially minimizing food waste.
As traceability becomes a more significant issue for the food and beverage industry — and major buyers like Walmart begin to require blockchain traceability compliance — a growing number of warehouse owners are likely to buy into the technology.
4. Autonomous Warehouse Robotics
The adoption of autonomous warehouse robotics has grown rapidly over the past few years. Industry experts have forecasted continued growth, and as many as 50,000 warehouses may use the technology by 2025.
These robotics take advantage of the latest advances in artificial intelligence to pilot themselves around the warehouse with minimal or no human interaction. Depending on warehouse needs, they may assist with picking orders, conducting inventory checks, or moving heavy pallets around the facility.
As the warehousing industry continues to struggle with its ongoing labor shortage, robotic solutions that assist floor staff, like autonomous mobile robots (AMRs), may become increasingly useful.
For companies that are having difficulty finding skilled employees, these robotics can offer a valuable stopgap — helping to ease the workload placed on current staff, while boosting productivity and making the warehouse easier to manage.
The use of AMRs by major warehouse-owning companies, like Amazon, may also encourage widespread adoption of these robotics throughout the warehouse industry.
There are some risks to heavy investment in the technology, however. Industry observers, for example, have raised concerns that in warehouses that implement these robotics — like those owned by Amazon — managers may be tempted to let the robots set the pace. This could encourage workers to move faster than they might otherwise — potentially leading to burnout or musculoskeletal injuries on a long enough timescale.
5. Remote Warehouse Management
The growing use of IoT technology will also make remote control of warehouse equipment much more practical. With the right equipment, like an IIoT device that can interface with warehouse machinery, it’s possible to check up on and even control warehouse equipment from anywhere in the world, so long as you have an internet connection.
This can help distributed office and administrative staff manage work on the floor and keep an eye on automated systems, like smart lighting or HVAC technology.
Remote access technology may also help make diagnostics simpler for warehouse owners. If a technician can access a robot or similar piece of equipment without traveling to the warehouse, they may be able to solve a problem with its functioning from miles away. This could help reduce the need for maintenance calls and potentially help managers avoid significant downtime.
The same tech would also give remote staff a view of machine health in warehouses that have adopted predictive maintenance tech, helping them know about potential future machine failure.
How Warehouse Automation Will Change in 2021
The growing availability of AI-powered automation technology — like AMRs and predictive maintenance — is likely to have the biggest impact on warehouse automation this year.
As it becomes easier to process the massive amounts of data that IoT sensors generate, we’re also likely to see the warehouse industry invest in these technologies. This, in turn, may inspire even more investment in solutions that can draw insights out of IoT-collected data and use it to automate warehouse processes.
Revolutionized is reader-supported. When you buy through links on our site, we may earn an affiliate commission. Learn more here.