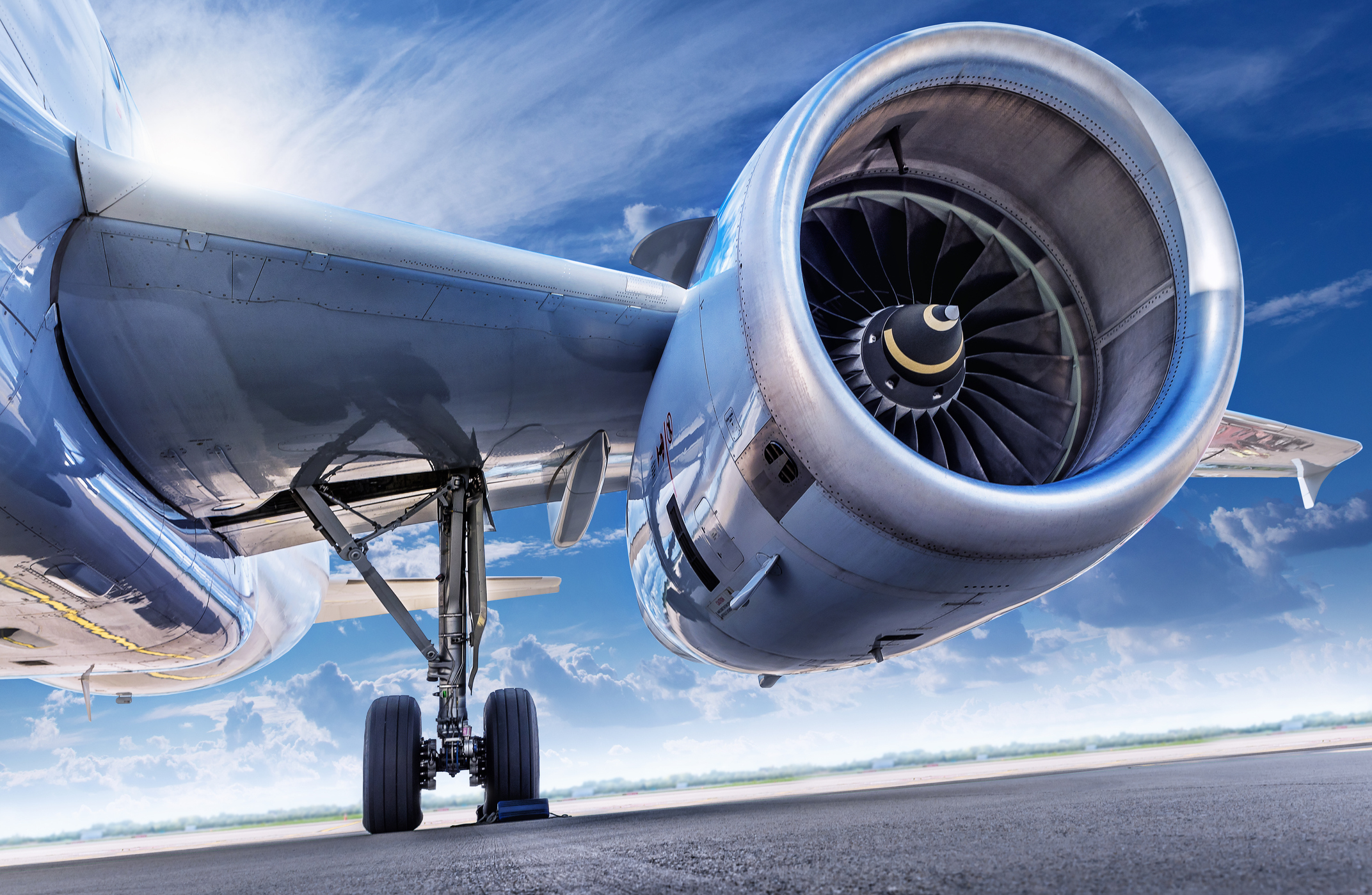
How Is Additive Molding & ARRIS Composites Improving the Molding Industry?
December 3, 2021 - Emily Newton
Revolutionized is reader-supported. When you buy through links on our site, we may earn an affiliate commission. Learn more here.
People are increasingly interested in how additive manufacturing will change the game for how product creation happens. A company called ARRIS Composites wants to push the boundaries even further with its patented Additive Molding process.
It uses additive manufacturing to make high-strength, lightweight composite products that are faster and less expensive to produce than conventional methods allow. Here’s a look at what ARRIS Composites does and why its methods could spur progress in numerous fields.
How the Additive Molding Process Works
The Additive Molding approach includes several steps, which result in products consisting of “continuous 3D aligned fibers”, such as carbon and glass, thermoplastics and any supporting components, like metallic inserts or electronics.
The first step is Preforming, which involves shaping the composite materials. That happens by inserting thermoplastics into continuous dry fiber and forming them as appropriate while covering them with resin. Then, those shapes get put together correctly in the 3D-Aligned Preform Assembly stage.
Finally, the Mold Processing phase enables finishing those assembled parts and checking them for accuracy and the desired performance attributes. This step also involves verifying the necessary surface qualities and ensuring the producers can achieve repeatability when making multiple parts.
Improving Strength With Continuous Fibers
One standout factor of the ARRIS Composites Additive Molding process is that it allows automating some aspects of production while providing the flexibility to put specific materials in certain regions of a part or change the material used.
Founder and CEO Ethan Escowitz also explained why the ARRIS Composites Additive Molding process brings strength beyond what conventional casting or 3D-printed parts can. Carbon-fiber components typically get made when people cut patterns in the shape of the desired components. However, the pioneering approach ARRIS uses features carbon strands that wrap all the way through the part and align with its stress vectors.
“When you are cutting out shapes, you are cutting fibers. That’s where we have the ability to do things differently,” Escowitz said. When speaking about the resulting parts, he noted, “We can make them more complex because we have greater resolution and shape control.”
It’s also helpful that the thermoplastic composite fibers used in Additive Molding offer room-temperature stability. Conversely, the regular “cloth” used for carbon-fiber parts has a stickiness and floppy feel.
Advancing the Aircraft Industry
Since ARRIS Composites can make customized parts that are strong and lightweight, it’s well-positioned to meet the demands of the aircraft industry. Thoughtful engineering is crucial for helping today’s planes fly. For example, the wings spread and elongate air, making it occupy a larger physical space. That effect happens, in large part, due to the curved upper part of the wing.
Making Better Cabin Brackets
Internal enhancements can make big differences too, as evidenced by a collaboration between ARRIS Composites and Airbus. Replacing metal aircraft cabin brackets with composite parts made with Additive Molding led to a 75% weight reduction in the components, translating into significantly better fuel economy for the planes.
The outcome is also substantial since hundreds of these brackets go into a single aircraft. Estimates associated with this project showed that manufacturing 100 planes with 500 brackets each would cause lifetime fuel savings equalling 113 million metric tons and a reduction of 357 million metric tons in CO2 emissions.
Bastian Schäfer, the innovation manager at Airbus, said, “The way we design and manufacture airplanes is changing because of emerging technology companies like ARRIS, who share and enable our vision of better air travel. We’ve known that biomimicry, topology optimization and advanced composites are the future, and ARRIS is helping us bring together these design and material ideals to manufacture the future of flight today.”
Bringing More Reliability to Drones
People are eager to learn how drones might play an even more prominent role in future society than they do now. For example, one company can deliver up to 2,500 doses of COVID-19 vaccines to hard-to-reach areas per day. That could revolutionize the distribution of medications and other lifesaving items, especially in less-developed areas.
However, it’s often challenging to design drones that are robust enough to carry their cargo, plus light enough for efficient flights. Additive Molding could help address that problem.
Applying Additive Molding to New Drones
When drone company Skydio worked with ARRIS to design its X2 models, the result was undeniably impressive.
CEO Adam Bry explained, “We are excited about the value that our partnership with Arris will bring to our customers. At Skydio, we pursue cutting-edge innovation across all facets of drone technology. The unique properties of Arris’s Additive Molding carbon fiber allow us to optimize the strength, weight, and radio signal transparency of the Skydio X2 airframe to deliver a highly reliable solution that meets the needs of demanding enterprise, public safety and defense use-cases.
While speaking of the partnership, Escowitz noted, “Such a moment has come where manufacturing of optimized structures has converged with composite materials ideals to unlock previously impossible, high-performance aerospace designs.”
He continued, “While we’re working with leading aerospace manufacturers to improve aircraft performance, sustainability and costs; Skydio’s culture and market have enabled an unsurpassed pace of innovation that has fast-tracked this transformation to deliver the next-generation of aerostructures.”
Creating Lightweight Combat Vehicles
There’s also ongoing interest in keeping military combat vehicles light while accommodating the increasing features that bolster safety and elevate user-friendliness. Unfortunately, as the overall number of vehicle components rises, so does the weight. ARRIS Composites recently brought its Additive Molding process to the U.S. Army to try and tackle this issue.
Tweaking Seats for Better Performance
The goal was to replace the metal component assemblies in the vehicles’ crew seats with composite pieces made through Additive Molding. This initiative is part of LIFT, a public-private manufacturing innovation partnership between the U.S. Department of Defense and various industry and academic participants.
Nigel Francis, LIFTs CEO and executive director, highlighted the potential outcomes of this endeavor. He said, “The real significance of a weight-savings approach for vehicle design depends on its broader applicability.”
Francis continued, “High-end, high-cost vehicles have lightweighting approaches that don’t translate to mass production and cost-sensitive industries. ARRIS’ unique ability to combine lightweight materials, lightweight structural designs, and cost-effective manufacturing is an important set of capabilities to drive LIFT strategic objectives.”
He then described how this approach should bring notable advantages, stating, “Our collaboration with ARRIS and the Army is an important step in lightweighting vehicle structures for the military and the competitiveness of the U.S. automotive industry as a whole.”
Escowitz echoed those sentiments, saying, “Working with LIFT and the Army to bring together advanced composites and advanced structural design in a key vehicle subassembly is an important step in advancing vehicle architectures. This pioneering work with LIFT will pave the way for broader adoption of lightweighting and realizing the associated performance, efficiency, and sustainability benefits.”
Enhancing Integrated Electronics Designs
The Internet of Things (IoT) industry has taken off in recent years. Products with embedded connectivity unlock opportunities to collect and receive data in industries ranging from manufacturing to mining.
Escowitz penned an article that revealed some of his hopes for future IoT products, as well as the role ARRIS Composites might play in helping them happen. In part of the piece, he described how electronics enclosures have gotten progressively more advanced.
He clarified, “That enclosure is an engineering marvel — resisting a long list of mechanical load scenarios and serving as an antenna, heat sink, user interface, environmental encapsulation, and doing so with extreme pressure to occupy as little volume as possible.”
Escowitz continued, “This exemplifies the state-of-the-art, highly integrated product designs for portable electronics that have paved the way for IoT designs. And in this space, the design and manufacturing ideal is locating the minimum amount of the ideal functioning material in the perfect place. Serving the needs of the design teams pursuing these ideals is ARRIS’ purpose, and our new design and manufacturing toolbox is how we do so.”
Accelerating the Potential of Future Electronics
The article also described how the ARRIS Composites methodology supports “…the pursuit of smaller, lighter, more rugged, better-encapsulated devices with demanding thermal and antenna requirements.”
Moreover, “Additive Molding opens all-new possibilities by enabling design teams to put different materials adjacent to one another within the same part. The right material, in the right place, in a single part.”
Escowitz then described some of the numerous benefits, saying, “By doing so, electronics, signal circuits, structural health monitoring, metallic components, damping, thermal requirement, cosmetics, and numerous other product requirements can be solved better than with today’s existing manufacturing methods.
What can manufacturers expect from such future-oriented processes? “One of the most common benefits these ‘better’ products realize is part count reduction through part consolidation and the associated product volume reduction,” Escowitz confirmed.
A Bright Future for Additive Molding
There’s an ongoing need for lightweight and strong components. ARRIS Composites offers a high-tech method to provide them, applying automation when possible while giving parts designers unprecedented flexibility in materials usage.
These characteristics strongly suggest the company will play a primary role in introducing forward-thinking industry leaders to its Additive Molding approach and how it surpasses traditional options.
Revolutionized is reader-supported. When you buy through links on our site, we may earn an affiliate commission. Learn more here.
Author
Emily Newton
Emily Newton is a technology and industrial journalist and the Editor in Chief of Revolutionized. She manages the sites publishing schedule, SEO optimization and content strategy. Emily enjoys writing and researching articles about how technology is changing every industry. When she isn't working, Emily enjoys playing video games or curling up with a good book.