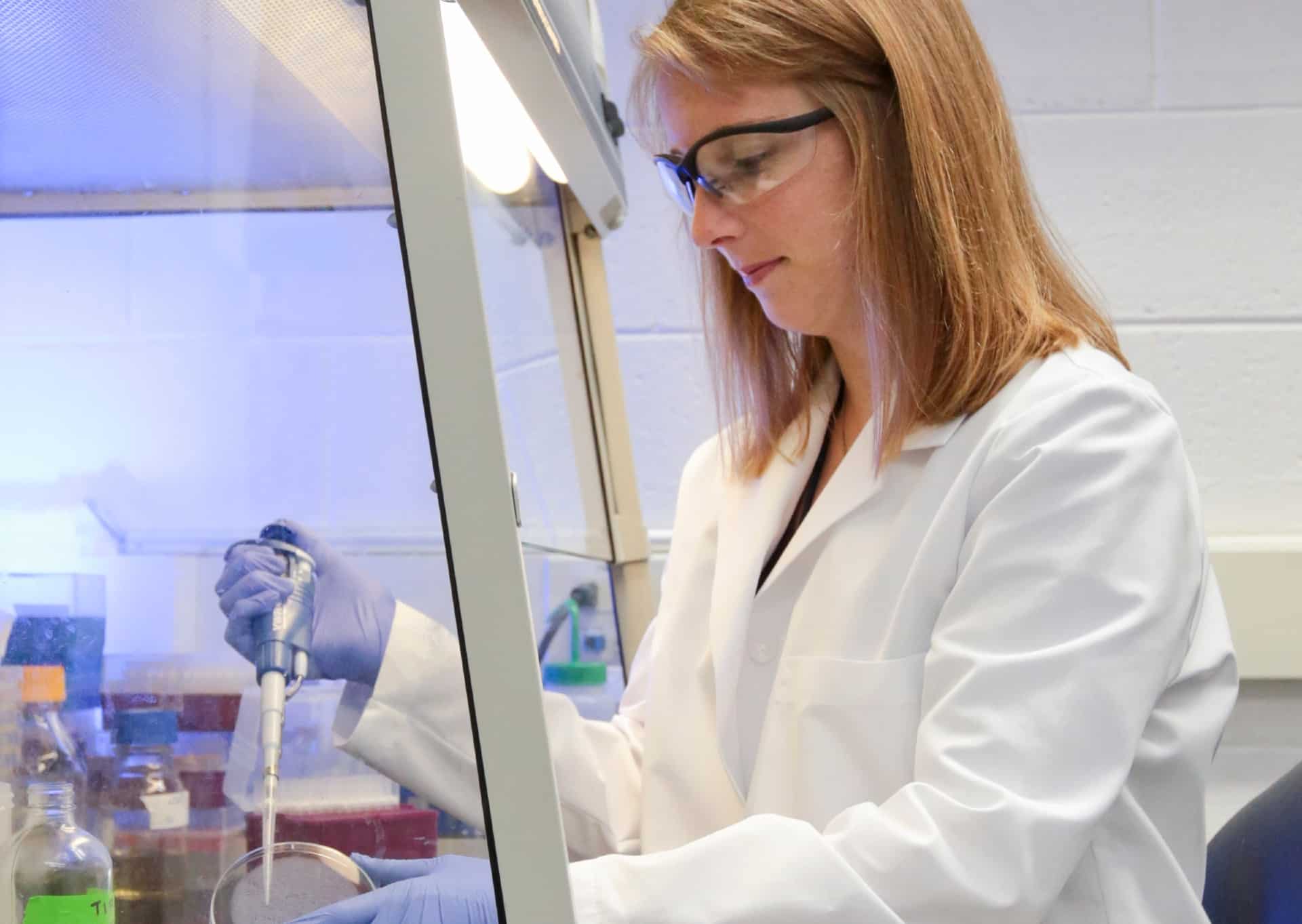
Here’s How to Successfully Make the Move to Bioprocessing 4.0
February 16, 2021 - Emily Newton
Revolutionized is reader-supported. When you buy through links on our site, we may earn an affiliate commission. Learn more here.
The idea of bioprocessing 4.0 evolved from industry 4.0, which people more commonly associate with broader manufacturing. When a facility moves ahead with a bioprocessing 4.0 strategy, it uses increasingly high-tech, interconnected and data-driven processes. Transitioning to incorporate this bioprocessing technology is not quick or easy, but company leaders can achieve progress by following some helpful steps.
Help Staff Understand the Potential Benefits of Bioprocessing Technology
Employees may initially feel hesitant when they get the news about transitioning to new ways of working. Some people fear automated technologies will replace their jobs. Others worry that data analysis platforms will eliminate humans’ need to use apply critical thinking skills.
Succeeding in a move to bioprocessing 4.0 requires helping workers how they’ll benefit. For example, if a factory has data-driven, automated elements, bioprocessing engineers could spend more time on the innovative parts of their roles than the tedious, frustrating ones. The same goes for bench scientists, who could save the time they usually devote to redoing assays or preparing plates.
Virtually all transitions go more smoothly when everyone’s on board with them. When employees see a new way of doing things, they’ll get more out of their work. This will help them become more eager about an upcoming factory revamp.
Areas to Improve Bioprocessing Technology
Those facilitating new bioprocessing 4.0 methods typically get the best results by prioritizing a few key areas of operations. Many decision-makers mistakenly try to implement multiple changes at once. It’s then more challenging to assess the impacts each one had on overall output or other goals.
Atul Mohindra, senior director of research and development at Lonza, gave a specific example of how bioprocessing 4.0 helped his company. “We recently implemented process analytical technologies at our plants. Adopting such technologies in the development stages of a program, we can use even smarter modeling tools to design and model processes.”
Mohindra also had a future-oriented mindset. “In addition, once these technologies are implemented, we will be able to generate vast amounts of data, which can be used for further purposes. But there are many other applications, such as the use of robots and data analytics for environmental monitoring in our facilities.” Whether a company wants to improve batch release time or avoid downtime with predictive maintenance, those things are possible. Choosing desired areas of improvement leads to satisfying results.
Sensors and Data Collection for Quality Control
The highly connected nature of a bioprocessing 4.0 facility creates opportunities to collect data and contribute to better quality control. Many data-collection platforms work remotely, which means a person can keep an eye on processes from wherever they are. Having such visibility can prevent complications while boosting productivity.
For example, dimethyl sulfoxide (DMSO) is the standard chemical compound for cell preservation. Moreover, it is hygroscopic and will absorb water from the atmosphere, making storage in a tightly closed container essential. Manufacturers usually recommend storing it in cool temperatures, too. Perhaps a bioprocessing facility has stored DMSO. In that case, intelligent sensors could collect data. They can give notifications if it stays outside an optimal temperature range for too long or someone neglects to reseal its container correctly.
Another example of how sensors could contribute to quality control is for bioethanol production. The widely accepted best temperature range for fermentation is from 30 and 35 degrees Celsius. Products exist that allow for the remote and real-time analysis of bioethanol fermentation. People can monitor it from a smartphone, tablet or computer, getting instant feedback if anything goes amiss. Any bioprocessing technology efforts should ideally include similar data-backed improvements.
Consider Investing in Custom-Built Equipment
Some bioprocessing decision-makers find that existing products on the market fall short of the mark. That may mean it makes economical sense to ensure that the budget contains enough money to cover customized equipment costs.
Andy Topping, CSO at Fujifilm Diosynth Biotechnologies, asserted that many automobiles and airplanes are better at generating data than most bioprocessing equipment. Not content with currently available options, representatives at his company piloted a continuous process at production scale for a 500-liter perfusion bioreactor.
After learning from that experience, the company worked with vendors and other partners to build a customized system from the ground up. They concluded it was easier to create an internal interconnected system than to invest in several independent options that may not seamlessly integrate. This case study illustrates why it may be necessary to buy customized equipment to get closer to bioprocessing 4.0 goals.
Aim to Achieve Continual Incremental Improvements
Making a move to bioprocessing 4.0 is not something a company should expect or aim to do in a matter of weeks. Instead, it requires a thoughtful plan occurring over many months — and perhaps years, depending on the undertaking.
No matter how entities decide to implement advanced technologies into their facilities, they should strive for incremental improvements. That way, they can avoid doing too much at once and becoming overwhelmed by all the newness or potentially misusing financial resources.
The tips here will help companies get off to strong starts on their bioprocessing technology journeys. Before implementing these suggestions, teams should understand the company goals and which metrics to use to gauge progress. Then, they can determine whether the hoped-for improvements are happening or if more tweaks are necessary to optimize the results.
Revolutionized is reader-supported. When you buy through links on our site, we may earn an affiliate commission. Learn more here.
Author
Emily Newton
Emily Newton is a technology and industrial journalist and the Editor in Chief of Revolutionized. She manages the sites publishing schedule, SEO optimization and content strategy. Emily enjoys writing and researching articles about how technology is changing every industry. When she isn't working, Emily enjoys playing video games or curling up with a good book.