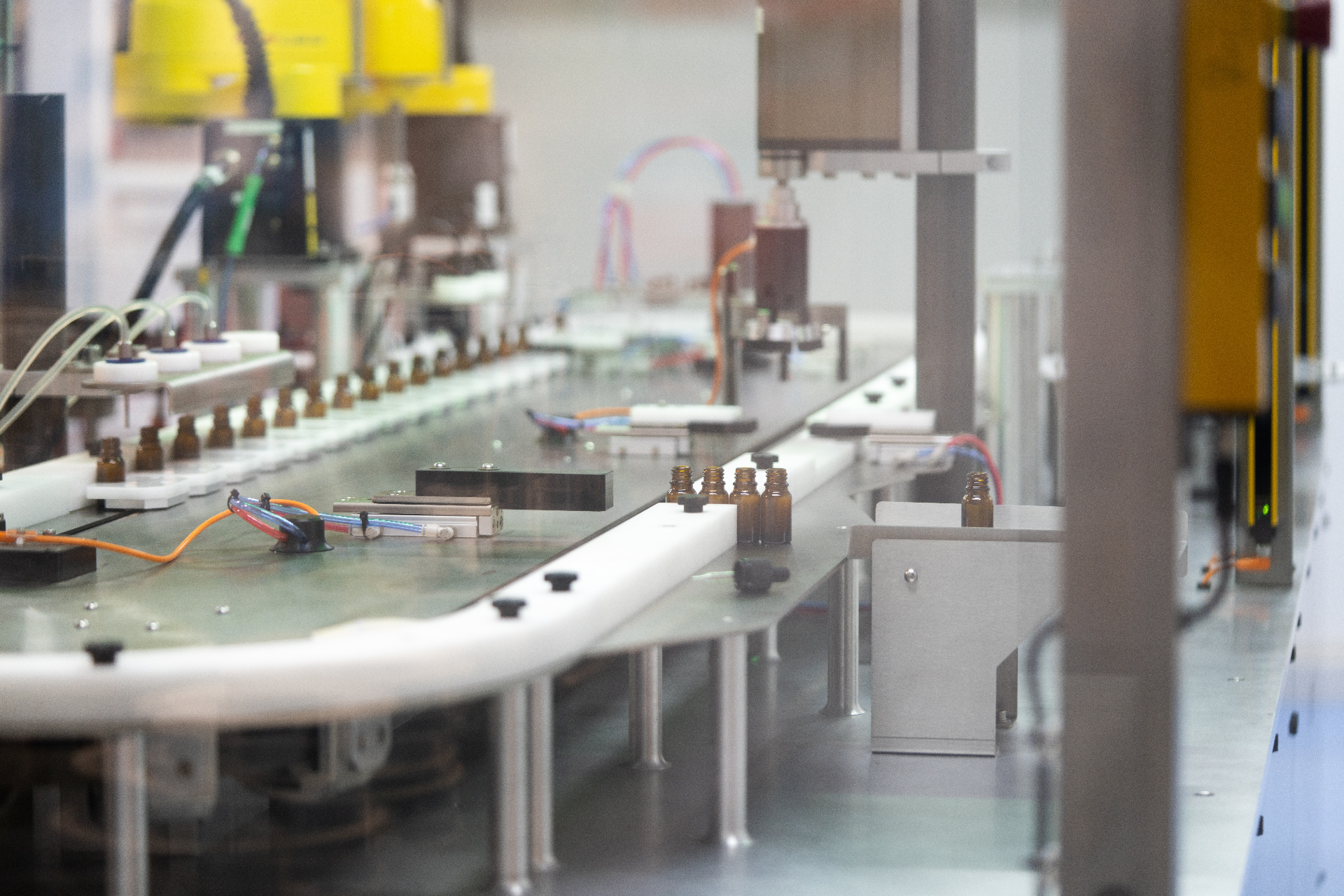
What Causes Downtime in Manufacturing?
July 13, 2023 - Emily Newton
Revolutionized is reader-supported. When you buy through links on our site, we may earn an affiliate commission. Learn more here.
Downtime in manufacturing is any time when the company or operators stop creating products. Output is at a standstill. There are various reasons for this, some within an organization’s control and others not. Enterprises must identify their top causes of downtime to analyze productivity and initialize procedural improvements and process discovery.
A manufacturing outfit that produces consumer goods versus lithium-ion batteries may have sector-specific reasons for downtime, but these will cover industry-agnostic causes for downtime in manufacturing.
Supply Loss
Loss of supply refers to interruptions in production because parts of entire products are delayed, missing, or understocked. It’s one of the broadest categories of downtime because of the sheer number of influences and hands that pass the materials through the supply chain.
Let’s start by looking at the supply chain. It’s not just tech that requires many parts, from specially-made circuit boards to LCD screens. Even shampoo bottles require specialty cap makers and various suppliers for different bottle sizes and colors. Manufacturers also need corrugate, packing material, and stretch wrap, among other supplies, to pack, load, and ship consumer goods. Manufacturing is a multi-step process, and every part has a unique supply loss possibility.
Third parties could experience raw material shortages that force delays in shipping. Communications from production line technicians to warehouses might need to be clarified between programs and parties, causing misunderstandings and wrong deliveries. When supply loss happens, downtime is inevitable until they find what got lost in translation.
Curtailment
Every manufacturing plant will see peaks and valleys of specific products. One might outpace sales one week, and another may plummet beyond expectations the next. So, a company may curtail manufacturing an item or range. Warehouses are already overstocked to the brim, forcing many megacorporations to build new warehouses to keep up — they can’t afford to shelve products that aren’t appealing to customers.
Therefore, a product-specific line might have downtime because that product halts production until they sell some of its backlogs. Alternatively, the planet may discontinue production of a product, causing downtime until the business reworks that line for another product.
One way to curb curtailment issues is to leverage data, Industrial Internet of Things (IIoT), and artificial intelligence. Machine learning algorithms can use predictive analytics to forecast what products will sell well or potentially catch a trend. It may reveal products sitting in warehouses are worth repurposing, donating, or disposing of instead of taking up space in the hope they’ll become relevant again. Data-driven solutions can guide misaligned manufacturing plants to use their stores better and have more resilient bottom lines.
Planned Maintenance
If the machine doesn’t work, then products fail to produce correctly. It’s impossible to expect a device that potentially makes thousands of products an hour to remain in tip-top shape without dedicated attention. Therefore, companies must plan for technicians to do regularly scheduled maintenance and compliance checks to report updates, failures and order replacement parts if necessary.
Though planned maintenance doesn’t look suitable for company metrics, in the long run, it saves budgets and time to invest in every machine’s health instead of waiting for a total collapse that requires an entire replacement — putting production lines out for much longer than several-hour maintenance jobs.
Plus, it becomes even more cost-effective and impactful by incorporating smart technologies that send notifications and perform rudimentary maintenance via automation.
Equipment and Material Failure
Despite constant oversight, sometimes machines fail. Production lines are chock full of sensors, which can force the machine to stop any disruption that could cause further damage to the product or machines. Not all technicians are perfect or adequately trained, meaning hiccups that initiate unwanted downtime in manufacturing will arise.
A way to remedy this is through training. The more aware technicians are about the machines, the more in-tune they can be to prevent things from going awry. Does a belt look slightly warped? Is there a new sound coming from inside the housing that’s unusual? Dedicating time to increase familiarity with the tech and products coming down the line can prevent unnecessary failure.
Sometimes it’s products that catalyze failures. For example, a third party could provide the cardboard that packages products. Suppose the third party sends over cardboard with defects preventing the machine from sensing or gripping it correctly on the line. In that case, that signals a material failure that technicians must contact third parties to fix. Until they obtain the necessary materials, they will have to shut down the lines.
Staffing Shortages
Lack of staff is another layered issue. The first is internal. Even if the line is at capacity with the ideal amount of workers, companies inevitably have meetings, evaluations, or audits that force workers to step away. The line can only run with oversight. Therefore, a team-building exercise or performance review might cause the line to shut down.
Additionally, a line might need more staff from normal circumstances, like leaves of absence or unexpected callouts. Most manufacturers need a minimum number of operators to manage the line, and if someone has to take a break, but that puts them below that grace, they have to go into downtime.
Another barrier is external. Despite higher pay rates in manufacturing compared to other sectors, factors like swing shift schedules and safety concerns make turnover relatively high. Over half of American manufacturing workers plan to get out of the industry by the end of 2023, and if conditions continue the way they are, the sector will struggle to keep top talent. Big picture influences, like the millennial push to college education over going into a trade, also directly impact how many skilled workers enter the manufacturing force.
It’s fewer than in previous decades, and the manufacturing worker shortage is a constant problem. These unintended consequences compound internal staffing shortages, adding up to an unfortunate amount of downtime in manufacturing.
Downtime in Manufacturing Can Stop
Sometimes, downtime is wanted. It allows technicians to grow and learn more about their work to create better products. However, usually, it reveals an opportunity to improve efficiency, productivity, or working conditions.
How can businesses entice workers to become tenure-track to fix staffing problems? How can enterprises engage with supplier diversification to ensure they aren’t burdened with the side effects of material shortages? These essential questions must guide the industry to reduce downtime only when required.
Revolutionized is reader-supported. When you buy through links on our site, we may earn an affiliate commission. Learn more here.
Author
Emily Newton
Emily Newton is a technology and industrial journalist and the Editor in Chief of Revolutionized. She manages the sites publishing schedule, SEO optimization and content strategy. Emily enjoys writing and researching articles about how technology is changing every industry. When she isn't working, Emily enjoys playing video games or curling up with a good book.