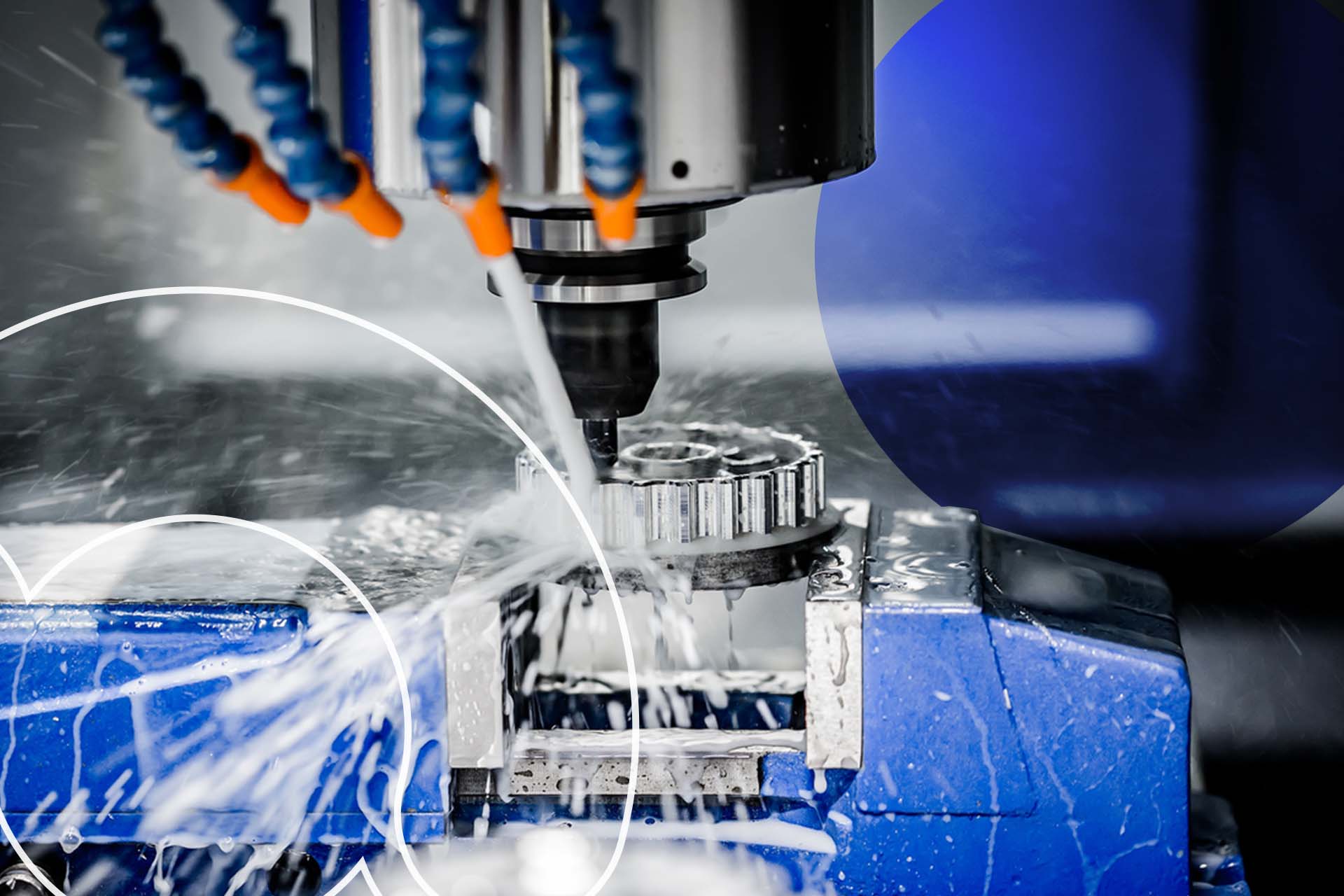
How to Improve CNC Machining Efficiency
December 12, 2019 - Emily Newton
Revolutionized is reader-supported. When you buy through links on our site, we may earn an affiliate commission. Learn more here.
Time is money, as the adage claims. In manufacturing, however, time is much more than that. CNC machining is fast-moving and highly competitive, so any operation must stay as efficient and productive as possible. One of the areas to optimize is CNC machine efficiency.
For most manufacturing networks, a project starts at the machining stage. Machinists pass on components, either to another in-house team or a third party to assembly them in bigger products. A slow process affects the entire supply chain, at least as it pertains to said components and goods.
Here are five ways CNC machining operations can improve their overall efficiency.
1. Upgrade or Retool Equipment
Old machinery and equipment lose efficiency over time — it’s just the nature of the game. Thanks to technological advancements over the last few years, that problem has improved considerably. Today’s equipment is much more powerful and efficient, and in many cases, it offers more opportunities — such as remote operation via mobile.
It’s necessary to upgrade equipment and systems to stay as close to the bleeding edge as possible. This is a difficult consideration for many teams, because machining equipment is not cheap. It takes both time and money to invest in new gear, not including the requirements for training personnel to use said devices.
Coming up with a protocol for replacing and retooling equipment is necessary. It can help define when and where to make upgrades, as well as set limitations on existing equipment. It may also be possible to retool or upgrade existing machines, as opposed to replacing them outright.
2. Push CNC Machine Efficiency and Tooling to the Limit
Today’s CNC machines were designed for high-performance, high-efficiency situations. In other words, they were meant to be run like a workhorse, almost nonstop and at maximum loads. That’s exactly why the above step is important. Keeping equipment new and in tip-top shape means you can continue to run it at maximum levels of performance. It can also help cut down on total machining time, which is the primary cost driver for all operations in the field.
As long as CNC machines are operational, they are one of the most profitable investments for any machining or manufacturing operation. When they’re idle, they’re a huge waste of resources and put a gap in overhead. It’s best to keep them operational and at max throughput.
3. Understand and Maintain Power Requirements
Machinery equipment and large-scale operations consume lots of power, that much is clear to anyone with experience in the industry. That also means it’s easy to underestimate power requirements, which could lead to serious issues and extended downtime. The last thing any operation wants to see is a power outage due to a demand overload.
Understand what power requirements are necessary to keep machining solutions operational. Maintain those needs, and continue to audit and assess requirements regularly. As new equipment is brought online, it may be necessary to scale up the power supply.
4. Establish Multiple Modes of Operation
The CNC gear will generally continue to operate on its own following a strict set of parameters thanks to sensors and load cells. There’s not always a need for personnel to sit directly beside the machine, leaving plenty of opportunities for parallel work.
Come up with multiple modes of operation, designed to make the best use of each worker’s time. Make sure teams always have a list of duties, so they know what and when they can move on to other tasks or projects.
This is something that can also be incorporated into each individual’s performance review. Team members that are going above and beyond, for instance, should be duly rewarded.
5. Real-Time Management Solutions for CNC Machining
Conventional maintenance and upkeep methods involve manually monitoring equipment and taking action when problems are discovered. Many times, this can lead to more of a reactive process — where crews are working to repair machines after they’ve malfunctioned. A more efficient way to handle this is through real-time and preventive maintenance strategies.
Modern data monitoring solutions can power this type of system. Imagine team members working to keep equipment in good shape, taking action based on a series of factors like declining performance or system errors. Monitor systems with AI or machine learning to analyze incoming data to understand and extract insights. It means the entire process can be automated from top to bottom — keeping efficiency as high as possible.
Modern Technology Plays a Huge Role
Improving efficiency and optimizing operations to maximize output means adopting modern solutions. Smart and IIoT-enabled machines can automate a great deal of the work while eliminating the mediocrity manual laborers have to deal with.
Preventive maintenance for operational gear can be powered by IoT and AI solutions to keep the entire team up and running. Better use of personnel time is another great solution. More equipment is upgraded for autonomy, which gives workers more time to complete other tasks.
By following the tips discussed here, machining operations can realize maximum levels of efficiency. Doing so will boost output, profits and employee satisfaction.
Revolutionized is reader-supported. When you buy through links on our site, we may earn an affiliate commission. Learn more here.
Author
Emily Newton
Emily Newton is a technology and industrial journalist and the Editor in Chief of Revolutionized. She manages the sites publishing schedule, SEO optimization and content strategy. Emily enjoys writing and researching articles about how technology is changing every industry. When she isn't working, Emily enjoys playing video games or curling up with a good book.