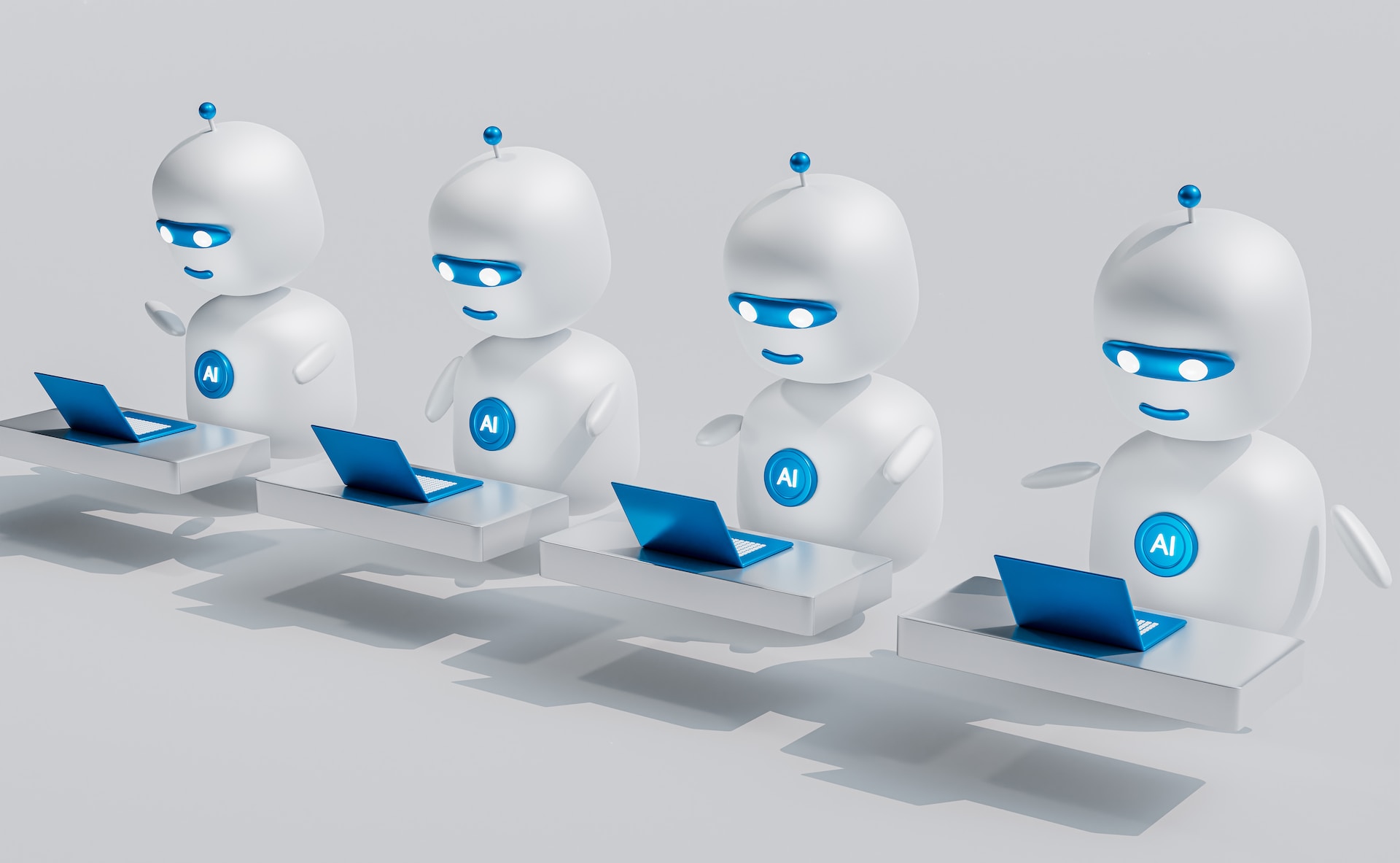
How Industrial Robots Impact Employees: Pros and Cons
June 20, 2023 - Ellie Gabel
Revolutionized is reader-supported. When you buy through links on our site, we may earn an affiliate commission. Learn more here.
Are industrial robots good or bad for employees? It may be more complicated than it seems. Automation is rapidly changing the workplace and the job market. Industrial robots offer some fantastic benefits for businesses, but it’s important to also understand the possible drawbacks.
How Industrial Robots Help Employees
There are some real ways that industrial robots can improve the workplace experience for employees. With the right robotics implementation strategy, employees can benefit from robots as much as employers do.
Filling Labor Gaps
Labor shortages and skill shortages are a serious issue in many industrial fields today. For example, the manufacturing industry is expected to have a shortage of 2.1 million employees by 2030. When jobs go unfilled, it puts more pressure on the few employees who remain. As a result, their jobs become more stressful and more risky.
Industrial robots can be a great solution to labor gaps. The jobs that are going unfilled are often physical labor roles that can easily be automated with the right robot. These jobs are also the least appealing to employees and job seekers. With robots in those jobs, recruiters can focus on advertising more rewarding positions.
Additionally, there isn’t a 1:1 ratio between robots to humans. Since robots are more efficient than humans in repetitive tasks, a single robot can take over several unfilled jobs. Plus, the greater efficiency of robots compared to humans goes a long way toward alleviating physical and mental stress on understaffed teams.
Reducing Physical Labor
Industrial labor jobs can include a lot of hands-on tasks, heavy lifting and long hours standing or walking. By adopting industrial robots, businesses can reduce the physical strain their employees experience on the job. This can reduce health insurance costs, injury rates and time off work related to injuries or illnesses.
Reducing physical labor can also make industrial jobs more appealing, potentially helping with labor shortages. For example, employees in a warehouse can have a courier robot bring them items to pack in boxes rather than walking around the warehouse all day. Now employees get to sit down for most of their shift, making this a much more relaxed job.
Demand for Upskilling and Reskilling
While industrial robots may eliminate some manual labor jobs, they do also create new jobs. This can result in employees getting opportunities for upskilling or reskilling, allowing them to move into higher-paying roles.
Surveys show that 68% of workers in America are willing to go through retraining to learn new career skills. This can take the form of upskilling or reskilling. Upskilling involves teaching employees more advanced skills related to their current job. Reskilling is more lateral and trains employees in a completely new job.
For example, when businesses adopt industrial robots, they need new employees who can repair and program the robots. Instead of trying to hire new people for these jobs, businesses can upskill existing employees who might otherwise be let go. This is a great way to prevent robots from “replacing” employees. Instead, automation simply moves people out of manual labor roles and into technical roles.
The Negative Impact of Industrial Robots
Industrial robots can help employees, but they can also have serious negative side effects. These range from complete job elimination to increased stress and anxiety. Robots are even changing the way some businesses treat and compensate their employees.
Mental Health Issues
Depending on how industrial robots are integrated in the workplace, they can result in negative mental health side effects for employees. For example, studies have found that robots can increase job insecurity fears. This means employees experience more fear of losing their jobs when robots are present in the workplace.
Robots can also lead to performance challenges that cause stress and anxiety for employees. Businesses may be so impressed by their robots’ performance that they put pressure on employees to meet the same standards. Humans are not robots, though. They can’t be expected to work at maximum speed or efficiency 100% of the time. This type of pressure can cause employees to experience depression, anxiety, stress and physical injury.
For example, Amazon’s warehouses and distribution centers all over the world use hundreds of industrial robots for a variety of tasks. Unfortunately, global studies show that Amazon’s productivity expectations are mentally and physically harmful for many employees. One Polish warehouse employee even commented, “We work with robots but we aren’t robots ourselves.”
Employers have to remember that people are not robots and it is not fair to expect employees to perform in the same way a robot would.
Reduced Value and Wages
Industrial robots can shift the way employers view the value of employees, potentially causing a reduction in wages. After adopting robots, businesses may see them as superior to employees due to higher productivity and a lack of basic needs like breaks, time off, healthcare and workplace safety. As a result, businesses may reduce employee wages in order to funnel more money into robotics investments.
While there is nothing wrong with investing in more industrial robots, it is important for businesses to be aware of where the money is coming from. Studies show that certain groups of people are disproportionately impacted by robot-induced wage reductions, particularly young people and people of color.
Industrial robots can be helpful for employees, but not if they result in lower pay that directly impacts employees’ well-being.
Job Elimination
Job elimination is a natural consequence of integrating robots in the workplace. Depending on the circumstances, this can have a negative impact on employees. If industrial robots are eliminating jobs that couldn’t be filled despite the best efforts of an employer, then the integration will likely be harmless to employment.
On the other hand, if robots are eliminating well-paying jobs that people do want, that can be an issue. Employers can mitigate job elimination by ensuring they create new jobs to replace those lost to robots. For example, they can upskill employees to become robot technicians instead of letting them go.
Should Businesses Adopt Industrial Robots?
Considering all of the pros and cons of industrial robots and their impact on employees, should businesses adopt these robots? Usually automation in the workplace is a great idea, but only with thorough planning that accounts for employees’ well-being. It’s definitely possible to integrate industrial robots in a way that benefits everyone, it simply requires some extra consideration.
For example, before investing in robots, businesses should analyze what tasks they would automate with the robots and how that automation would impact employees. If jobs would be eliminated, the business could make a plan for upskilling or reskilling the affected employees.
Businesses also need to carefully separate productivity expectations for employees and robots. Each has their own strengths, but pressuring employees to achieve the same speed and productivity as a robot is simply unsafe. Doing so can lead to serious mental and physical health consequences and even permanent injury.
Before bringing robots into the workplace, employers should take steps to make sure automated areas have safety systems in place. Additionally, employees should all receive some amount of robot safety training. It is also helpful to provide employees with resources or a contact person they can reach out to if they are struggling with mental or physical challenges due to the addition of robots in the workplace.
Adopting Industrial Robots the Right Way
In the workplace of today and tomorrow, robots and humans have to be able to work in harmony, not competition. When adopting industrial robots, businesses have to take steps to ensure automation aids employees rather than hurting them.
Robots can cause mental illness, physical injuries, job insecurity and other negative side effects if not integrated carefully. With the right preparation, though, industrial robots can reduce physical strain for employees, help out understaffed teams and create new job opportunities.
Revolutionized is reader-supported. When you buy through links on our site, we may earn an affiliate commission. Learn more here.
Author
Ellie Gabel
Ellie Gabel is a science writer specializing in astronomy and environmental science and is the Associate Editor of Revolutionized. Ellie's love of science stems from reading Richard Dawkins books and her favorite science magazines as a child, where she fell in love with the experiments included in each edition.