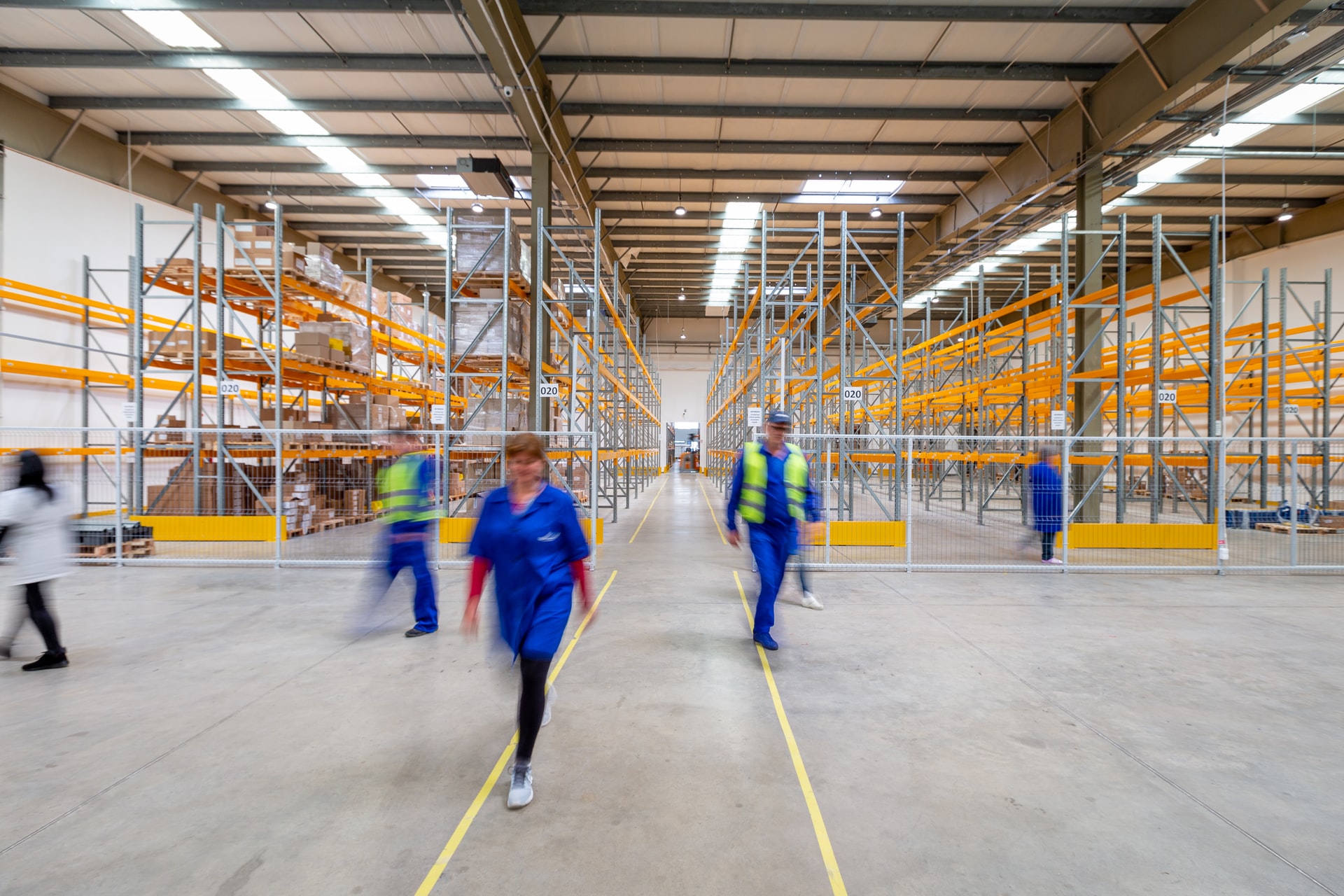
Your Instructive Guide to Warehouse Order Picking Methods
August 2, 2022 - Emily Newton
Revolutionized is reader-supported. When you buy through links on our site, we may earn an affiliate commission. Learn more here.
All warehouses use order picking methods to ensure quick and orderly retrieval of goods from storage. Otherwise, fulfillment processes can easily become disorganized — especially in warehouses that deal with a large number of orders every day.
A variety of order picking methods exist, each with its own set of advantages and disadvantages. A warehouse’s size, equipment, technology and customer base can all influence which order picking method will work best.
These are eight of the most common order picking methods.
1. Single-Order Picking
The most common order fulfillment method, single-order picking (or discrete order picking) is also the least efficient. As the name suggests, single-order picking means picking one order at a time. Pickers will search the warehouse for each item in an order. Then, they’ll pick these items one by one until the order is complete.
As a result, pickers will travel the same route for much of their shift. They may need to make multiple trips to fill several orders that they could have completed in one trip.
Because pickers work on just one order at a time single-order picking can improve picking accuracy over other picking methods.
For smaller, low-volume warehouses, this picking method can sometimes be useful. However, larger warehouses can often benefit from more sophisticated and efficient picking methods.
2. Batch-Order Picking
With batch order picking, warehouse pickers will work on multiple orders at once. Pickers will work on one SKU (type of item) at a time. As a result, they won’t have to travel to an item location more than once per picking cycle, helping to reduce travel time.
This method is otherwise similar to single-order picking.
The batch-order method is a good fit for warehouses that regularly fulfill orders with the same items. The more complex and varied orders become, the fewer benefits a warehouse will see from switching to batch-order from single-order picking. If a warehouse stocks a wide variety of SKUs, batch-order picking may not be that much more efficient than single-order picking.
3. Zone Picking
With this order method, the warehouse organizes its pick area into several distinct zones. Warehouse managers assign pickers to a zone. Pickers will be responsible for picking all SKUs in their zone. Workers often pick multiple orders at the same time.
If an order contains SKUs from multiple zones, a picker will complete only their part of the order, then pass the order to the next zone. In some cases, they may store partially complete orders in containers or bins that they will pass to the next zone. This method is also called the “pick and pass” method as a result.
Zone picking is generally more efficient than single-order or batch-order picking. The method can also reduce travel time and floor congestion. However, zone picking can also unevenly distribute work across the warehouse. If one zone is much busier than another, one picker may be struggling to keep up with work while another may be virtually idle. Effective management of pickers across zones will be necessary to reduce inefficiencies.
4. Cluster Picking
With the cluster picking method, workers pick into multiple order containers (or “pick clusters”) at the same time. These containers may be totes containing order batches, discrete order totes or discrete order shippers.
Typically, these containers will be loaded together on a large cart or similar piece of equipment for easy movement around the warehouse.
Pickers, rather than focus on a specific SKU, will pick a variety of items at the same time for multiple orders. As a result, the cluster picking method will reduce travel time, but not by as much as batch-order picking.
To make moving and loading containers easily, pickers may sometimes be supported by automated warehouse equipment, like autonomous robots, that will perform basic picking work.
5. Wave Picking
Depending on the implementation, wave picking can be extremely similar to cluster picking or zone picking.
With wave picking, a system releases new orders to the floors in short picking intervals (or waves). The system groups orders by characteristics like shipping date, warehouse zone and SKUs.
Warehouse pickers will use a tote or container to pick all items for the order. Next, they’ll send this group of items to another group of workers that will organize, package and ship them.
Dividing the workday into waves can help managers identify staffing issues, scheduling inefficiencies and other problems that may not be as obvious with other picking systems in place.
6. Mixed Systems
Many warehouses will implement a combination of the above systems, depending on their particular needs, picker availability and warehouse configuration.
Common examples of these systems include zone-batch and zone-wave picking. These systems are similar to the batch and wave methods, but additionally divide the warehouse into zones of related SKUs to streamline the picking process. Some warehouses may also combine zone, batch and wave picking systems.
As systems become more complex, however, they can introduce new problems. Both managers and pickers may make mistakes more often the more information they need to keep track of.
7. Pick-to-Light Order Picking
A pick-to-light order system uses colored light modules to direct workers to the right SKU or zone for each order, The color and placement of the lights will tell workers which item and how much to pick.
More conventional pick-to-light systems use red and green light bars that are hard-wired into warehouse flow racks, shelving or similar equipment. More modern systems may use wireless cloud-connected lights, often LEDs, to provide more information to workers.
The method allows for fast order picking without a paper or digital list, as all the information that a worker needs to complete and order will come from
The system is easy to learn and allows workers to pick orders quickly, even if they’re not familiar with the warehouse’s layout. For warehouses with regular turnover or seasonal fluctuations in picker numbers, this system can help improve the productivity of new workers.
Pick-to-light systems can be expensive, however. The pick-to-light method may also be slower than other methods for particularly small orders.
A pick-to-light system will generally build on another picking method, like a batch-order or zone picking system. The lights will replace the physical or digital lists that workers previously relied on with these systems.
8. Voice Order Picking
With a voice picking system, workers receive voice prompts that direct them to the items that they need to pick for an order. These voices prompts are generally delivered via a hands-free headset that workers will wear while on the warehouse floor. The voice prompts themselves are generated from a combination of pre-recorded voice clips and speech synthesis.
Like pick-to-light order picking, this order picking method enables quick order picking without a digital or paper list. It can help accelerate training for new workers and ensure that seasonal or temporary pickers will be able to easily find the items they need to complete every order.
As with pick-to-light systems, however, voice order picking systems can be expensive. Headsets can also create new safety issues. If workers can’t hear what’s going on around them, they may be less able to respond to potential safety hazards, like forklifts and other heavy machinery.
Also like pick-to-light systems, voice order picking generally modifies an existing system, like a zone picking system.
How Warehouses Choose Their Order Picking Methods
Efficient picking systems can be hard to design, especially as supply chain disruptions and rising customer expectations become the norm.
Warehouses use a variety of different picking systems to facilitate fast and accurate order picking — ranging from simple single-order systems to highly complex zone-wave systems.
Some warehouses also use voice order picking and light systems to replace more conventional picking lists.
All of these systems can help a warehouse improve picking operations and ensure the speedy fulfillment of orders.
Revolutionized is reader-supported. When you buy through links on our site, we may earn an affiliate commission. Learn more here.
Author
Emily Newton
Emily Newton is a technology and industrial journalist and the Editor in Chief of Revolutionized. She manages the sites publishing schedule, SEO optimization and content strategy. Emily enjoys writing and researching articles about how technology is changing every industry. When she isn't working, Emily enjoys playing video games or curling up with a good book.