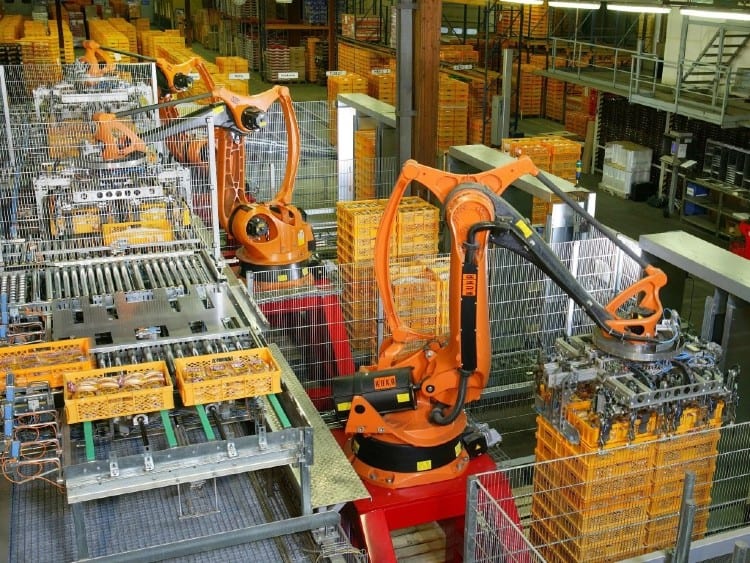
Everything You Need to Know About IoT in Manufacturing
January 9, 2020 - Emily Newton
Revolutionized is reader-supported. When you buy through links on our site, we may earn an affiliate commission. Learn more here.
The Industrial Internet of Things is enjoying widespread adoption throughout the industrialized world. It is also, justifiably, considered one of the lynchpin technologies of the Fourth Industrial Revolution. Steam power vaulted industrial manufacturing technology forward once before. The impact of the IoT in manufacturing could be even more pronounced as we explore its potential.
So how exactly is the Internet of Things being used across the manufacturing landscape? And which factors are driving this development? Let’s find out.
How Is the IoT Used in Manufacturing?
Consider the human body. Without our really being aware of it, our bodies shuttle nutrients, oxygen, blood and other resources throughout the body constantly or on-demand. There are systems in place, like the circulatory and endocrine systems, that regulate these functions. They ensure they happen when they should and according to the right internal and external conditions.
These systems function independently, but they ultimately answer to the central nervous system. The IoT is a little like a central nervous system for industrial environments, complete with sensory “organs” for gathering information about environmental “stimuli.”There isn’t any one simple answer to the question, “How is the IoT used in manufacturing?” But with any luck, this analogy gives you an idea of the implications.
Above all, what the Industrial Internet of Things provides is distributed computing and improved awareness of the factory or machine shop floor. Distributed computing means assets like material handling equipment and vehicles can gather data on their own performance. They can analyze it onboard, oftentimes without dialing home to a server.
The connectivity this provides between industrial equipment (hardware) and enterprise management platforms (software) unlocks tons of cost-saving and resource-saving functionality. This gives manufacturers opportunities to improve collaboration between business partners.
Let’s look at some of these implications right now.
Practical Applications for the IoT in Manufacturing
In a 2016 report, the Information Technology & Innovation Foundation (ITIF) estimated machine monitoring applications would improve global manufacturing productivity up to 25% by 2025. They estimate this would add $1.8 trillion in value to the world economy. That’s a huge feat! So how is the Internet of Things going to make it happen?
“Machine monitoring” is a broad concept. Below we elaborate on the three main categories where the IIoT helps cut costs, increase productivity and economic value like the ITIF spoke of in their report.
1. Industrial Asset Tracking
Monitoring the way machines are utilized is beneficial for any industry. In manufacturing, tracking industrial assets is important because it reveals what’s happening at every step in every process. It reveals bottlenecks and helps anticipate work stoppages due to poor planning or equipment that’s out of place.
The IoT offers several protocols for tracking industrial assets in real-time. These include Wi-Fi, Bluetooth, RFID, NFC, MQTT and Ethernet for stationary equipment. Bar codes and QR codes are also more than adequate for many processes and operations.
In a manufacturing setting, industrial asset tracking is used to determine the location as well as the condition of things like:
- Stationary manufacturing equipment
- Lift trucks and automated guided vehicles
- Palletizers and material handling equipment
- Totes of raw materials or finished or unfinished products
- Handheld tools and portable equipment
2. Predictive Maintenance
Quite often, it’s not the physical location of a manufacturing asset that needs real-time tracking. Unless you’re hand-assembling your goods for a small audience, you probably rely on complex powered tools and equipment.
Like the central nervous system receiving sensory input before or after an injury, the IoT likewise receives and provides insight into machine health. A Deloitte report predicts the IoT will yield a 40% reduction in equipment maintenance costs and add $630 billion to the global economy by 2025.
There was a time when manufacturing equipment didn’t even come standard with an Ethernet port. Today, even some of the most complex equipment has built-in telemetry features so operators can better understand their machines and deliver proactive maintenance.
In some cases, like with cooling tanks and mixing equipment, it’s especially important to use the most advanced monitoring equipment available — like the IoT. Having the means to monitor critical equipment for leaks, contamination, scale buildup, corrosion or compromised performance can make the difference. These have a direct impact on product quality and employee and customer safety.
The IoT monitors machine health by observing the operation of the equipment, including its efficiency, temperature, and any unusual movements or sounds. Then, it tips off the maintenance crew about the potential issue, so they can get to it fast and check it out. In the case of refrigerated goods or foodstuff manufacturing, response time is especially critical.
Using the IoT to understand and optimize machine health applies to a number of industrial manufacturing equipment categories, including:
- Industrial generators
- Mixers and centrifuges
- Holding and mixing tanks
- Coolers and boilers
- Chillers and refrigeration equipment
- Lifts, conveyors and warehouse vehicles
- Packaging machinery
3. Industry Management
The IoT in manufacturing culminates in next-generation industry management.
Industry management means different things to different companies. Ultimately, it’s about achieving synergy among in-house processes and synchronicity with business partners upstream and downstream in the supply chain. When the shipping department reduces its downtime by keeping its packaging dispensers online longer, or AGVs slash fulfillment errors by supplementing human order pickers, the whole company benefits.
Likewise, individual manufacturing facilities that invest in IIoT technology make themselves more efficient and valuable supply chain partners. All of the data generated by manufacturers helps fine-tune strategic and management decisions in the supply chain.
For instance, using the IoT to provide inventory visibility and sharing it with business partners helps them better anticipate your demand. It also gives them the means to have shipments ready to go just as they’re needed.
In other cases, the data breadcrumb trail provided by the IoT can help pinpoint where product defects may have occurred. This could speed-up product recalls, or potentially prevent the handoff of faulty products altogether.
Are There Any Challenges With the IoT?
As manufacturers explore their options, there are some challenges to be aware of as well.
One of these is security. Established manufacturers may be able to invest in in-house IT talent with up-to-date knowledge on cybersecurity best practices. If this isn’t the case for you, make sure you ask potential IoT service vendors how they’ll keep your data and infrastructure safe.
The lack of knowledgeable and qualified employees is its own challenge with the IoT in manufacturing. There is a learning curve associated with some of the value-adding hardware and software the IoT offers. It’s important to find technology partners with clear documentation, product demos and responsive technical support.
It can be a challenge to know what technology is worth the investment, too. For help with that, remember to talk with department leads and subject matter experts within your company. Make sure you understand your company’s “problems” and “opportunities” before reaching out to a company for third-party “solutions.”
Revolutionized is reader-supported. When you buy through links on our site, we may earn an affiliate commission. Learn more here.
Author
Emily Newton
Emily Newton is a technology and industrial journalist and the Editor in Chief of Revolutionized. She manages the sites publishing schedule, SEO optimization and content strategy. Emily enjoys writing and researching articles about how technology is changing every industry. When she isn't working, Emily enjoys playing video games or curling up with a good book.