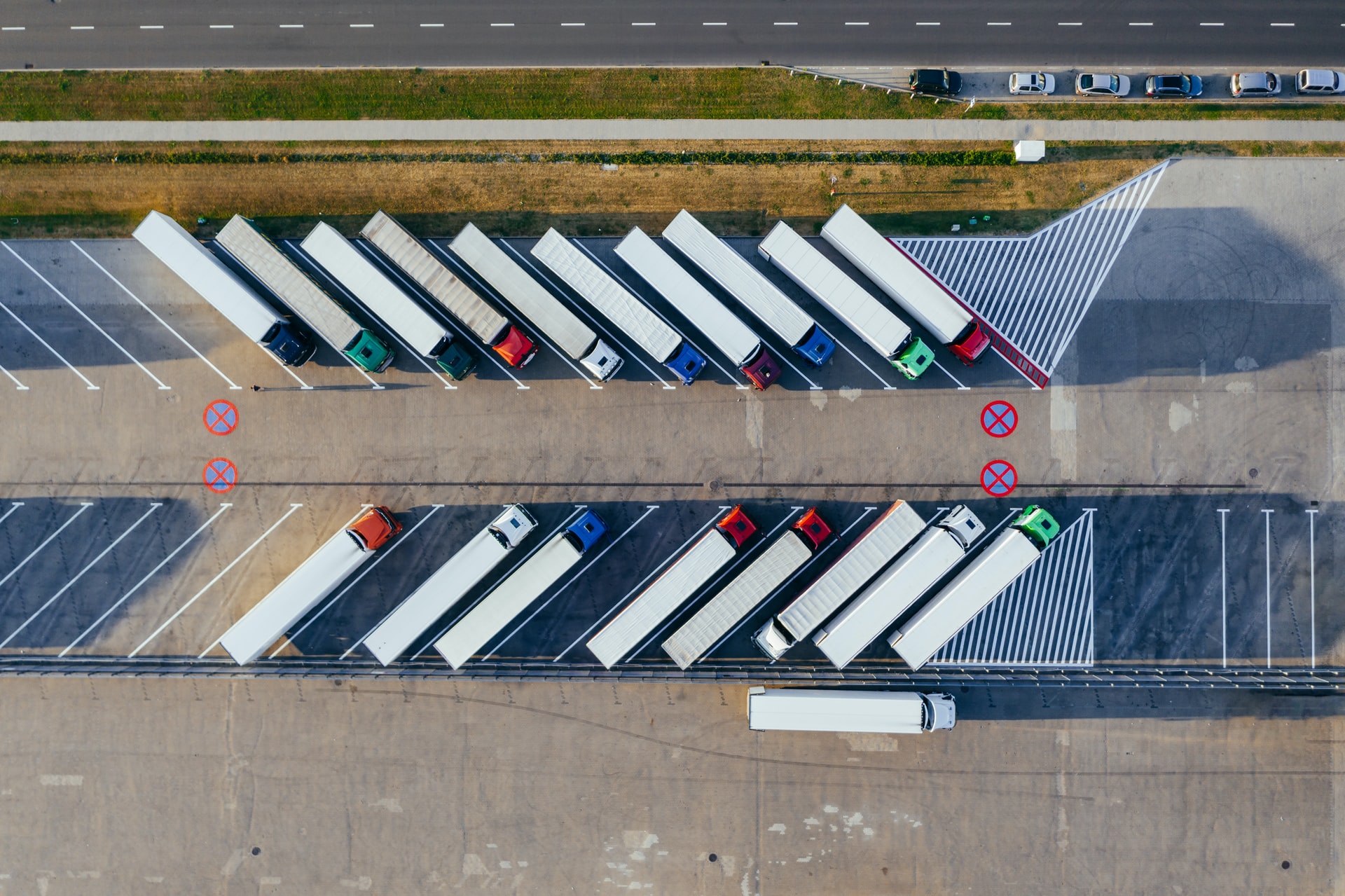
Balancing Upstream and Downstream Supply Chains
July 19, 2022 - Ellie Gabel
Revolutionized is reader-supported. When you buy through links on our site, we may earn an affiliate commission. Learn more here.
Supply chains are complex, so organizations often split them to make them easier to manage. One of the most common of these divisions is between upstream and downstream supply chain operations, separating sourcing and distribution processes.
While upstream and downstream operations share some factors, such as shipping and warehousing, they often look fairly distinct. However, it’s easy to take these divisions too far and treat each supply chain as an entirely independent network. If businesses want to optimize their supply chain operations, they need to bring these two halves together.
Why Balancing Upstream and Downstream Supply Chains Matters
Materials, money and information all flow between upstream and downstream supply chains. Consequently, changes in one chain will affect the other in one or more of these three critical areas. If organizations balance their upstream and downstream operations, these things will flow more smoothly, but if they’re too separate, they’ll hinder them.
Here’s a closer look at how balancing the two halves of the supply chain optimizes operations.
Minimizing Disruptions
The most important reason to balance upstream and downstream supply chains is to mitigate disruptions. Many of the largest supply chain disruptions arise from discrepancies between these two halves. The bullwhip effect, which can cost companies millions of dollars, is an all-too-familiar example.
Limited visibility or misunderstandings over downstream supply chain factors can cause upstream processes to over or underreact. Sudden demand spikes can create shortages if manufacturers don’t anticipate them. Then, these upstream parties may overcompensate and ramp up production too much, creating surpluses as downstream demand dies down.
These scenarios wouldn’t be as common or disruptive if downstream and upstream operations worked more closely. Upstream processes could adapt to downstream factors faster and more accurately, avoiding shortages and surpluses. If a disruption does arise, both halves could mitigate it by working together to offer a faster, more appropriate solution.
Maximizing Efficiency
Enabling smoother flows between upstream and downstream supply chains also improves efficiency. With more accurate, timely information from downstream operations, upstream processes could adapt to meet changing needs. As supply chains become more efficient, they’ll avoid unnecessary costs and increase profits.
Reducing disruptions like the bullwhip effect has a direct impact on savings. Decreasing the bullwhip effect ratio by one translates into $26 in inventory savings per product per year. That could add up to considerable profit increases over time and with enough products, and that’s for relatively small changes.
When upstream and downstream processes work more closely together, it’s also easier to map out logistics operations. Businesses can see how materials and products flow between suppliers and end-users and reorganize their supply chains to close distances. Shipping times and expenses will fall as a result.
How to Manage Upstream and Downstream Supply Chains
Balancing upstream and downstream supply chain operations is key to making these networks more resilient and efficient. Here’s how organizations can achieve this balance.
Maximize Visibility
The first step to bringing these supply chains together is increasing visibility between them. This part of the dynamic is often what businesses struggle with the most and, consequently, where the most disruptions arise. Just 6% of companies have full visibility into their supply chains, and a third have sold out-of-stock items due to this lack of transparency.
Upstream operations need to have accurate and timely insight into downstream activity to avoid disruptions. Organizations can provide that insight by using data technologies like cloud computing and the internet of things (IoT). These technologies can gather information like sales figures, transportation statuses and consumer trends that upstream manufacturers can respond to.
Businesses can also use artificial intelligence (AI) to find relationships in large datasets, turning this data into actionable insights. That can include revealing sales cycles and demand shifts as well as existing inefficiencies. Organizations will gain a complete understanding of their downstream and upstream operations as a result.
Communicate Often and Thoroughly
It’s also crucial that upstream and downstream parties communicate with one another. Improving data gathering processes downstream will provide limited value if upstream facilities can’t see that data. Similarly, downstream partners should know about any upstream disruptions so they can react appropriately.
The best way to manage this information sharing is to provide a single source of truth for all parties. Cloud platforms can consolidate all relevant information in one remotely accessible dashboard. Using a single cloud solution instead of several disparate systems will keep everyone on the same page, preventing miscommunication.
Remote collaboration tools like videoconferencing software and instant messaging platforms are also helpful. These provide more engaging or timely updates than email, helping downstream and upstream teams communicate efficiently. Companies can also schedule regular meetings on these platforms to encourage consistent communication.
Enable Flexibility
Both supply chains must also be flexible. If upstream suppliers can’t scale their production quickly, demand insights from downstream sellers are of little value. Increased visibility and communication are the first steps towards this flexibility, but supply chains must go further.
Diversification is one of the most significant steps companies can take to enable supply chain flexibility. Instead of sourcing from a single supplier, organizations should have multiple sources, ideally in different areas. That way, disruptions at one won’t affect the entire supply chain, and businesses can adjust their orders from each to meet changing demand.
Thankfully, many companies are already moving in this direction. As of late 2021, 55% of supply chains embraced dual sourcing for raw materials, and 23% have expanded backup production sites.
Consider Vertical Integration
Some organizations may be able to join their upstream and downstream supply chains more than others. If it’s financially feasible, businesses should consider acquiring companies in their upstream or downstream operations. Bringing these once separate parts under the same company will offer more control and make it easier to gain a cohesive view of the supply chain.
This vertical integration typically reduces costs and turnaround times but involves a fair amount of risk. Organizations should review their options to see if it makes financial sense for their situation. If not, they can try to achieve similar benefits by maximizing communication and collaboration across supply chain partners.
Optimize Supply Chains Through Collaboration
Upstream and downstream supply chains may be separate entities, but they influence each other too much to keep apart. Organizations that can bring these networks together can create more flexible, resilient supply chains. They can then maintain productivity and surge ahead of the competition despite any disruptions that arise.
Revolutionized is reader-supported. When you buy through links on our site, we may earn an affiliate commission. Learn more here.
Author
Ellie Gabel
Ellie Gabel is a science writer specializing in astronomy and environmental science and is the Associate Editor of Revolutionized. Ellie's love of science stems from reading Richard Dawkins books and her favorite science magazines as a child, where she fell in love with the experiments included in each edition.