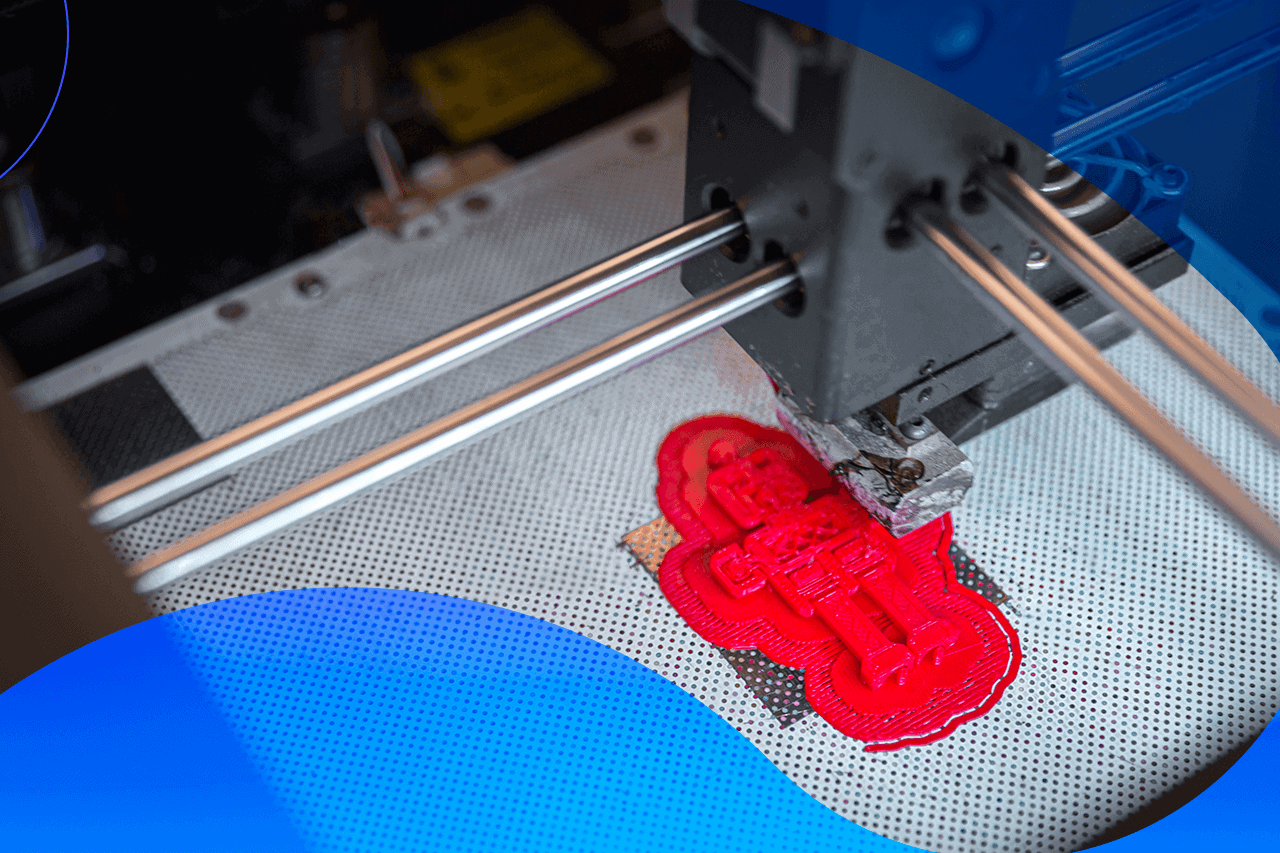
3D Printed Electronics Are Transforming How Electronics Are Made
August 22, 2022 - Emily Newton
Revolutionized is reader-supported. When you buy through links on our site, we may earn an affiliate commission. Learn more here.
Of all the major innovations to reshape industry over the past few years, one of the most important has been 3D printing. 3D printing provides a valuable alternative to conventional, subtractive manufacturing techniques. The approach, which is typically much faster and easier to retool than conventional manufacturing setups. It’s used in a variety of ways across manufacturing, including for rapid prototyping and small-batch manufacturing. We can create many things now like 3D printed electronics and 3D printed prosthetics and more.
Recent innovations in 3D printing tech, however, mean that it’s becoming easier and easier to print more advanced components with the right printer — including circuit boards and complex electronics. Now, the new technology may be on track to revolutionize the industry and reshape how electronics get made.
How to Create 3D Printed Electronics?
Most modern approaches to creating printed circuit boards, integrated circuits, chips and similar electronic components are subtractive in nature. With a printed circuit board, using a combination of techniques and following a master pattern, the manufacturer strips or etches material away from the surface of the board or circuit.
This approach often requires serious investment in both machinery, materials and reagents — like copper-etching solvent — and can generate significant waste.
3D printing, as an additive approach to manufacturing, typically creates less waste — because you’re adding material as needed. The alternative is starting with more than you need and cutting away. Then less material tends to end up unused. The approach is also often more cost-effective when manufacturing at a smaller scale.
3D printing in the electronics industry emerged from 2D printing of circuit boards using techniques like inkjet and aerosol jetting. These techniques apply electronic ink to a prepared substrate, allowing manufacturers to quickly fabricate devices and components ranging from transistors to complete solar panels.
By layering these 2D-printed components, it’s possible to create more and more complex devices.
Creating Electronic Devices With 3D Printing
It’s also possible to 3D print electronic devices from scratch by carefully alternating filament types and adding in components during the printing process to fully encase electronics in a device.
This approach to creating structural electronics is similar to the process for most 3D printing. A manufacturer begins by loading the material that the printer will use for printing, also called the filament.
Then, following a digital model of the object that it will print, the 3D printer slowly deposits the material in layers. It will stop as needed for the manufacturing team to swap out materials — or, in the case of electronics manufacturing, embed pre-manufactured components.
Through the use of recent additive manufacturing innovations — like new, specialized printing filament that can act as electronic wiring — the 3D surfaces of printed devices themselves can also be functionalized. This enables manufacturers to take full advantage of the material that would typically only be used to support or encase electronic components.
A recent case also allowed researchers to 3D print copper solderable circuits. They can create printed rigid or flexible printed circuit boards with up to four layers.
In another example, researchers at MIT opened new possibilities for printing electronics when they used a 3D printer to integrate breadboards directly onto physical products for enhanced prototyping. The breadboards are flat platforms with holes drilled into their surfaces. Electronics engineers can then put electronic components into the holes while choosing various desired arrangements. The results can help them determine optimal board layouts.
A company called Nano Dimension also wants to bring the 3D printing of circuit boards to the mainstream. It can print several types of them in one step.
Key Benefits of 3D Printed Electronics
These 3D printing approaches offer a few key benefits for manufacturers that adopt them. Here are some of them.
Better Agility
As in other industries, additive manufacturing will primarily help to enable more agile manufacturing, and provide manufacturers with an approach better-suited to on-demand and small batch fabrication.
Improved Efficiency at Better Prices
In general, 3D printing can do a lot to speed up the manufacturing process and make it much, much cheaper.
The BMW Group relies on 3D printing to create metal and plastic parts for Rolls-Royce automobiles. Representatives indicated this method enabled creating components with complex structures that were too cumbersome to manufacture with traditional processes. Such innovations can make certain approaches to manufacturing much more practical. Another company printed an astounding 60,000 components in only eight hours. That feat demonstrates the tremendous efficiency of this method.
3D printing also tends to be much more cost-effective than conventional manufacturing techniques at smaller scales. This makes small-batch runs of a particular device or product much more affordable than it would be with subtractive manufacturing. With a lower per-unit manufacturing cost, you won’t have to produce and sell as many devices to make the manufacturing process worth it. Rolls-Royce only makes a few thousand vehicles annually, making 3D printing a viable option.
More Customization Capabilities
The low cost of manufacturing means that customization may also be more cost-effective. With some devices, like medical electronics, it’s often not practical to manufacture a device for each patient, even if it would make the device more effective. 3D-printing can help manufacturers offer customized items like these to customers. It also may make specialty medical devices more affordable. Consider that researchers figured out how to print a focused ultrasound device for approximately $80.
Enhanced Sustainability
The 3D printing process can also make manufacturing more sustainable overall. In one instance, researchers developed a way to make Internet of Things (IoT) sensors with a 3D printer using a substance derived from wood cellulose. The primary benefit is that end users could dispose of the sensors without contributing to environmental contamination. People familiar with the matter also say 3D printing can cause a 70-90% reduction in scrap waste.
Rapid Prototyping Electronics With 3D Printing
For the electronics industry, one of the most significant benefits of 3D printing may also be in rapid prototyping.
In many industries, rapid prototyping is already helping manufacturers quickly test and iterate on new product designs. Because 3D printing doesn’t require any significant retooling of the manufacturing process, once a design is ready, it may be possible for a manufacturer to move immediately to printing a prototype.
With this prototype, the designer can better work out product ergonomics or see how a 3D printed object will stand up to strain in practice.
For electronics manufacturers, it means that they may be able to print a board, test it in-house and redesign that board multiple times a day. They may also test the function of more complex products, seeing if a functionalized 3D surface, for example, will be effective in practice.
3D printing circuit boards and similar electronics can also reduce the lead time on a project. Often, the manufacturing time and cost of a board will increase based on its complexity. With 3D printing, however, cost and time is more dependent on the size of the board and the amount of materials used.
This means that, if a design is ready, additive manufacturing may enable developers to quickly move to the prototyping stage with minimal lead time.
How The Industry Is Using 3D Printed Electronics Right Now
While the 3D printing of electronics is mostly experimental, scientists and businesses have already started to use the tech for practical manufacturing or research purposes. Here are some exciting examples.
3D-Printed Satellites
CubeSats are miniaturized satellites, made from cubic modules of a standardized size. They are a low-cost alternative to traditional satellites, and can be outfitted with commercially available electronics that are easy for student researchers to access. 3D-printed CubeSats have quickly become a powerful tool for scientists engaged in space research.
3D-printed CubeSats take advantage of a material called polyether ether ketone (or PEEK), a thermoplastic with strength and temperature resistance comparable to some kinds of metal. With added nanomaterials to the plastic filament, it’s possible to make PEEK electrically conductive.
As a result, it was possible to print functionalized portions of the CubeSat body that doubled as the satellite’s wiring. This approach can potentially increase the space available for electronic components or reduce the overall weight of the satellite — allowing researchers to develop easier-to-launch satellites or do more with the modules they can afford.
A related 3D-printing innovation involved creating a thruster for CubeSats. It’s about the size of a dime and generates a few dozen micronewtons of force. That’s about half the weight of a sesame seed. It may not seem like a lot, but people working on the project believe it could help. That’s because even a small amount of force could help a miniature spacecraft move, particularly in an environment without air friction.
A Flexible OLED Display
Researchers also used a 3D printer to make a fully flexible organic light-emitting diode (OLED display. They’re high-quality options used for large products, such as televisions. Many smartphones also include OLED displays.
The team relied on six different printing methods to make the display. It’s about 1.5 inches on each side. One of the researchers also indicated they could put the display in various encapsulating materials. That option greatly expands how people might make other products relatively soon. This 3D printing process might seem relatively complex. However, the people who developed it hope to eventually make it accessible to users who have 3D printers in their homes.
Other Innovations
In addition to electric wiring, researchers and manufacturers have also experimented with embedding electronic components directly in 3D-printed objects, like fully-encased capacitive sensors, meander-shaped resistors and solenoid-type inductors.
Some 3D-printing tech has also enabled the production of complex, multi-layer electronic circuits.
Future Applications of 3D Printed Electronics
In the future, an even wider range of applications of 3D printing tech may be possible. For example, one of the more unique possibilities of 3D printing tech is in stretchable electronics, which may be on track to disrupt the growing wearables industry.
With stretchable electronics, it’s possible to print electronic devices — like sensors and circuits — that can be stretched or compressed without being damaged.
These could act as an alternative to mass-produced wearable devices, which can often fail to conform to the particular physiology of a consumer or patient — making the wearable uncomfortable or hard to wear.
With affordable 3D printing tech, it may be possible to print new wearable devices on-demand that are tailor-fit to a particular patient’s body, helping to ensure maximum comfort and ease of use.
How 3D Printing May Reshape Electronics Manufacturing
3D printing has already had a major impact on the manufacturing industry at large — making it possible to manufacture goods with less waste or produce prototypes rapidly. Printing electronics is still not common everywhere. But, as more companies and individuals experiment with it, the potential use cases will become more apparent.
In the near future, 3D printing is likely to transform how electronics manufacturers approach their work. Functionalized 3D surfaces, faster prototyping and stretchable electronics are all made possible by 3D printing, and could have a major impact on the electronics industry.
The electronics sector is fast-moving and depends on people exploring new ways to do things better. 3D printing is only one example of a potentially game-changing technology. But, the associated progress certainly warrants further research.
Editor’s note: This article was originally published on April 8, 2021 and was updated August 22, 2022 to provide readers with more updated information.
Revolutionized is reader-supported. When you buy through links on our site, we may earn an affiliate commission. Learn more here.
Author
Emily Newton
Emily Newton is a technology and industrial journalist and the Editor in Chief of Revolutionized. She manages the sites publishing schedule, SEO optimization and content strategy. Emily enjoys writing and researching articles about how technology is changing every industry. When she isn't working, Emily enjoys playing video games or curling up with a good book.
This is such an interesting read! It’s amazing to see how 3D printing is moving beyond traditional manufacturing and making electronics more efficient and customizable. The examples like CubeSats and stretchable electronics are super exciting and show just how much potential this technology has. Can’t wait to see how it evolves in the future!