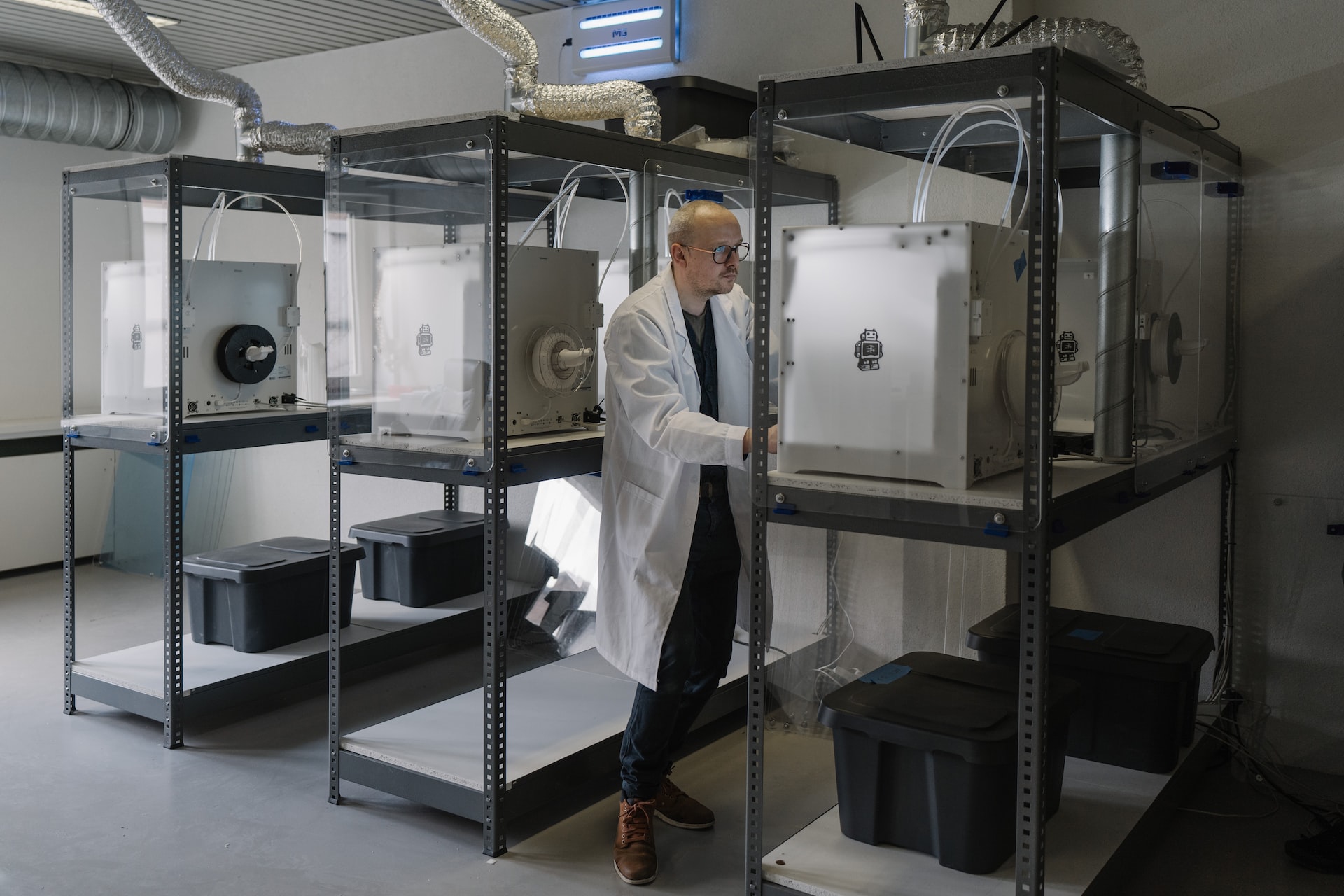
What Does It Take to Effectively Design for Additive Manufacturing?
February 5, 2023 - Emily Newton
Revolutionized is reader-supported. When you buy through links on our site, we may earn an affiliate commission. Learn more here.
Additive manufacturing – you probably know it as 3D printing – is unlocking new techniques, designs, and innovations throughout the industrial world. You might’ve experimented with a 3D printer yourself to create a model or possibly print replacement parts for a piece of equipment, like a lawn mower.
3D printing can be faster, less wasteful, and more convenient than conventional manufacturing, but it requires careful consideration. Design for additive manufacturing (DfAM) is a design method that accounts for the strengths and limitations of the 3D printing process itself and focuses on several characteristics of the end product, including:
- How reliable will the product need to be?
- How expensive is the product to produce?
- What level of durability or strength is required?
- How much material should the product use?
- Which features of the product make it ill-suited to conventional manufacturing?
Let’s dive deeper into design for additive manufacturing, starting with why it’s necessary.
Why Is Design for Additive Manufacturing (DfAM) Necessary?
Additive manufacturing already has several advantages over conventional manufacturing methods like CNC machining, casting, injection molding, and others. Additive manufacturing is capable of fabricating a component or finished product directly from its 3D digital model, building it layer by layer. This is fundamentally less wasteful than, say, a milling machine, which achieves the desired shape by cutting away material – which is oftentimes discarded – from the workpiece.
Compared to more traditional fabrication methods, 3D printing is better able to handle complex shapes that conventional equipment can’t reach, like inaccessible corners, hollows, and other forms of convoluted geometry. Because of this, additive manufacturing supports a degree of creative freedom that previous methods could not.
To fully capitalize on these capabilities, machine operators and product engineers need to know how to tailor their designs for additive manufacturing.
What Are the Principles of Design for Additive Manufacturing (DfAM)?
There are several principles and methods associated with design for additive manufacturing. They center on the capabilities of 3D printing and use DfAM to unlock new design potential.
In most cases, achieving optimized product designs under the DfAM philosophy will require a little outside help. We’ll provide a roundup of some digital design programs that specialize in design for additive manufacturing and provide tools for automatically applying these principles to your digital models. Topology optimization, for example, relies on mathematical calculations that would be extremely difficult to do “by hand.”
For simpler designs, like those made by hobbyists, it’s possible to implement some of these considerations yourself. Let’s explore the most important features of design for additive manufacturing.
1. Topology Optimization
Topology optimization relies on complex mathematical formulas to optimize the distribution of a material within a fixed design footprint. This process will, for example, consider desired end-product characteristics like load limits, boundary constraints, and other limitations, and generate digital 3D models that meet the requirements with a homogenous distribution of printer filament material.
This is different from shape optimization because, during topology optimization, the shape of the product may change to accommodate the other desired characteristics.
2. Multi-scale Structures
3D printers are uniquely capable of creating complex and helpful shapes known as “multi-scale complexities” or multi-scale structures.” You might’ve noticed this DfAM principle already in the form of honeycomb or lattice structures within 3D-printed parts.
Due to their tiny, repeating structures, these micro-scale or meso-scale shapes cannot be obtained using a conventional subtractive manufacturing apparatus like a mill or lathe. With a 3D printer, however, an engineer can deploy such methods to, among other things:
- Reduce the weight of an otherwise solid component (as in aerospace or automotive manufacturing, where every fraction of an ounce counts).
- Add multi-scale structures to the interior of a component to give it additional rigidity (helpful in situations where the end product will see deployment in harsh conditions).
- Enhance the ability of 3D-printed grafts and implants to achieve osseointegration (where living bone successfully integrates with an artificial structure).
3. Consolidation of Parts
The opportunity to consolidate two or more parts into a single component is one of the most appealing advantages of 3D printing and design for additive manufacturing.
Conventional manufacturing, as we’ve been discussing, has limitations. It’s often necessary for engineers to split up especially complex or specialized components into one or more components because they can’t be fabricated effectively, or at all, by the limited mechanical processes of CNC machines, lathes, and drills.
Consolidating parts using 3D printing and DfAM is where the product is redesigned to transform multiple adjacent parts into one. It’s possible to carry out this redesign by hand, but CAD programs equipped with DfAM principles can do the heavy lifting for you. The result is a part that’s cheaper and easier to produce, and oftentimes stronger than the multi-component version of the same structure.
4. Multi-Material Designs
3D printers are better able to fabricate multi-material designs than any previous manufacturing technique. This is because it’s simple to replace the printer filament – resin, ABS plastic, aluminum, gold, etc. – partway through the assembly process with a different or complementary material. Some printers are capable of holding and dispensing multiple filaments without a changeover.
Most CAD systems designed for conventional manufacturing don’t provide assistance when it comes to multi-material design implementation. It’s highly likely you’ll need to adopt a new software suite if you’re planning to go all-in on 3D printing and want to prioritize multi-material fabrication.
5. Support for Mass Customization
Another way DfAM is impacting the overall product-design process in manufacturing is through mass customization. Before 3D printing, there really wasn’t a way to engage in the mass customization of manufactured goods. Thanks to the additive process and the speed of 3D printers, that barrier has fallen.
Using DfAM with mass customization in mind might involve the addition of sockets or mounting points, or the creation of more modular product designs, to keep the majority of the fabrication process identical until the last 10 yards, when the customization process is applied to individual workpieces.
What Programs Support Design for Additive Manufacturing?
As mentioned, not every CAD program designed for conventional manufacturing can take advantage of all of 3D printing’s advantages. If you’re in the market for new digital design software, you’ll want to know it’s future-proof enough to support DfAM. Here are a few top choices:
- Altair Inspire Print3D
- Ansys Additive Suite
- Creo
- Fusion 360
- MSC Apex Generative Design
- nTopology
- Oqton 3DXpert
- Siemens NX
- Solid Edge
- Solidworks
You’ll want to take careful note of which applications provide simulation capabilities. Although 3D printing offers a host of advantages, it’s not the best fit for every product or manufacturing situation. A well-designed design for additive manufacturing program can create realistic simulations to help you determine whether additive manufacturing is the best way to create that item.
How Can I Study About and Learn Design for Additive Manufacturing?
If you’ve looked at the course catalogs for industrial design and engineering colleges, you’ve noticed that 3D printing – and its design principles and challenges – have become an important part of the core curriculum. 3D printing is growing rapidly; market forecasters predict the additive manufacturing industry will be worth $83.90 billion in 2029. That’s a huge leap from 2021’s $18.33 billion.
There’s no reason you need to enroll in a full-time university to study design for additive manufacturing, although you have lots of options. There are several ways you can engage in self-directed or instructor-led DfAM training. Here are a few:
- American Society of Mechanical Engineers DfAM With Metals: Self-directed online course; costs $195.
- Autodesk Generative Design for Manufacturing: Self-directed online course; costs $250.
- MIT Additive Manufacturing for Innovative Design and Production: Self-directed online course; takes 12 weeks to complete; costs $2,995.
- America Makes DfAM for Metals: On-premises learning at Youngstown, Ohio, or at your place of work; price on request.
- Wohlers Associates’ Design at Elevation Design for Additive Manufacturing Course: Three-day course; location varies; costs $2,995.
- Tri-Tech 3D DfAM Course: Two-day course taking place in Worcester or Stoke-on-Trent in England; price on request.
These design for additive manufacturing training modules and courses cover everything you need to understand to receive the associated professional certification, including cost calculations, material and shape optimization, post-processing tasks, and material science.
Kickstart Your Additive Manufacturing Career
After furthering your education, you’ll belong to a select group with highly specialized skills and a good degree of job security. Manufacturing will need lots of highly skilled 3D printing specialists, material science experts, and product design geniuses in the coming years. Older manufacturing employees are retiring in large numbers and there aren’t always enough young people with the relevant skills and certifications to replace them.
If what you’ve learned here today about 3D printing and design for additive manufacturing intrigues you, this could be an ideal moment to get your foot in the door with this fascinating technology. From 3D-printed homes to jewelry and circuits and much more, this is an exciting time for additive manufacturing indeed.
Revolutionized is reader-supported. When you buy through links on our site, we may earn an affiliate commission. Learn more here.
Author
Emily Newton
Emily Newton is a technology and industrial journalist and the Editor in Chief of Revolutionized. She manages the sites publishing schedule, SEO optimization and content strategy. Emily enjoys writing and researching articles about how technology is changing every industry. When she isn't working, Emily enjoys playing video games or curling up with a good book.