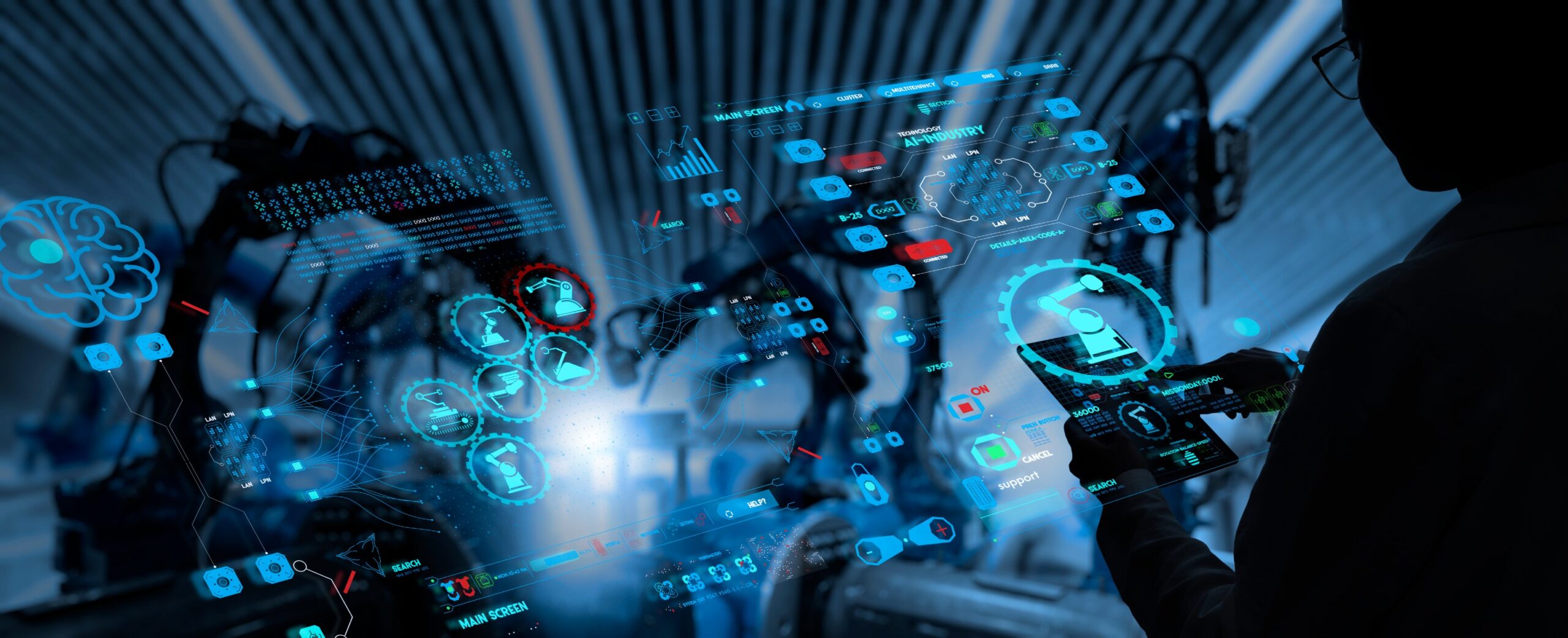
Industry 5.0: Everything You Need to Know
May 4, 2023 - Emily Newton
Revolutionized is reader-supported. When you buy through links on our site, we may earn an affiliate commission. Learn more here.
Modern industry periodically goes through progressively advanced stages with well-defined characteristics. For example, people discussing Industry 4.0 often mention data analysis, artificial intelligence, and smart or autonomous systems. To really understand Industry 5.0, we need to understand our roots.
Computers became prominent during the Third Industrial Revolution, and Industry 4.0 capitalized on them. It urged decision-makers to rely on data more than instinct and aggressively explore technological implementations.
The Fifth Industrial Revolution doesn’t discard those attributes. Instead, it focuses on humans working alongside highly advanced machines. There’s also a greater emphasis on sustainability and societal benefits rather than primarily profit growth.
Review: What Is Industry 4.0?
Industry 4.0 focused on ramping up the use of technology, including artificial intelligence, digital workflows and robots. Many of the associated goals in those transformations centered on driving economic growth, output and speed for the companies involved. Decision-makers also explored machine-to-machine communication and new connectivity methods to streamline their operations.
Data collection, processing and actionable usage were also foundational parts of Industry 4.0. Company leaders who did those things well knew they needed to get data from within and outside their organizations — and not just from the factory floor. It meant gathering and utilizing information from all a company’s departments and external partners, such as suppliers and logistics specialists.
Many company leaders explored options to upskill their workforces as Industry 4.0 gained momentum. Employees with increasingly technical skills became more valuable assets, especially if they could attend to a company’s high-tech equipment when problems arose. Workers’ training also changed, with many enterprises investing in virtual reality platforms and personalized learning tools to help them grasp and retain new concepts.
What Is Industry 5.0?
Industrial revolutions typically concentrate on what leaders should do for optimized results. Industry 5.0 explores how human-machine interactions can help companies reduce errors, increase output and become consistently more competitive in challenging, changing marketplaces. However, it’s important to recognize that this scenario has machines supplementing — not replacing — human effort.
There’s also a shifted focus from shareholder to stakeholder value. Profits are not entirely out of the equation, of course, but companies are more invested in what they can do to support the greater good. That often means corporations will have in-depth sustainability campaigns and make resource reduction a significant part of overall operating goals.
Worker well-being also lies at the heart of production in the Fifth Industrial Revolution. Robotic exoskeletons and employee wearables are two technologies that can support employees working and feeling their best while on the clock.
How Is Industry 5.0 Different From Industry 4.0?
Industry 4.0 and 5.0 have some similarities. For example, they both revolve around the increased use of advanced and connected technologies. However, many Industry 4.0 workers stayed largely separated from machines like robots, sometimes only interacting with them while a safety cage acted as a constant barrier.
Industry 5.0 will see the increased use of cobots — machines that can safely work around and directly with humans. Some companies already use cobots on assembly lines. Fiat invested in several to bring ergonomic benefits to employees assembling electric cars.
Whereas Industry 4.0 centered on economic value, the Fifth Industrial Revolution prioritizes societal value and the planet’s long-term sustainability. That said, are we in Industry 5.0 now? Not yet. Most companies are still in the Fourth Industrial Revolution and have yet to adopt the next industrial revolution fully.
Who Is Industry 5.0 For?
Industry 5.0 is for decision-makers who recognize the need to keep pace with competitors. That doesn’t mean adopting new technologies and operational methods immediately, but it requires being open to the possibilities and thinking seriously about implementing them.
Manufacturing is well-positioned to take advantage of Industry 5.0’s benefits, particularly as company leaders explore coping with growth challenges and increasing customer demands.
There’s also the case of the United Kingdom’s Aston University, which will collaborate on an Industry 5.0 project with an architectural hardware company. Estimates suggest the joint effort will cause a $12.4 million increase in turnover five years after this 24-month agreement ends.
The Pillars of Industry 5.0
Industry 5.0 is still a relatively new and emerging concept, and definitions vary. However, the European Commission released information about its vision for what the Fifth Industrial Revolution entails.
It breaks down into three areas: sustainability, human-centeredness and resilience. The information also clarified that research and innovation are vital drivers for the transition from Industry 4.0.
Here’s a closer look at each of the three pillars:
Sustainability
This broad category requires people to make changes within and outside their businesses. For example, they might use smart sensors to reduce water and electricity use within a factory. However, operating sustainably might also mean only working with suppliers and other partners who agree to meet specific eco-friendly standards.
The circular economy will also play a defining role as people explore Industry 5.0 technologies. Company decision-makers will more frequently pursue options to recycle their products, make them last longer, and help people return faulty or end-of-life items.
Human-Centeredness
The days of people doing mind-numbing work while standing for hours at assembly lines may be in the past with Industry 5.0. That’s because there’ll be more emphasis on giving humans tasks that connect to their abilities, problem-solving skills and creativity. Even the most advanced industrial robots can’t match the brainpower people have.
Expect more of a focus on assigning people to do tasks they find genuinely rewarding and interesting. Cobots can help fill the gaps, letting employees get more done with the same output.
Resilience
Improving resilience means ensuring companies are less affected by external shocks. Many businesses got wake-up calls during the COVID-19 pandemic, and the recovery phase is ongoing. Resilience also involves having enough flexibility and resourcefulness to spot trends or changes in demand and respond to them.
It’s also important to realize that many business leaders want to work toward these pillars simultaneously. A 2023 Accenture study found 66% of leaders were forming strategic partnerships to boost resilience. That same investigation revealed 98% of CEOs believed sustainability was core to their roles.
The Benefits of Industry 5.0
Decision-makers may initially balk at deploying Industry 5.0 technologies but become more upbeat once the advantages are apparent.
Most Customers Have Shopped for Sustainable Products
Companies could see their profits grow by embracing the Fifth Industrial Revolution, particularly regarding sustainable products. A 2023 Blue Yonder study found 74% of respondents had shopped at green retailers within the last six months. About 69% said they would pay more for eco-friendly offerings.
Business leaders must steer clear of anything people may perceive as greenwashing. However, customers should respond favorably if they can show a committed response to operating more sustainably.
Elsewhere, a study from McKinsey and NielsenIQ found that products backed by environmental, social and governance (ESG) claims showed 28% cumulative growth over five years versus 20% for companies that did not make such statements.
Still, consumers are getting more skilled at detecting whether a company’s leadership truly cares about sustainability or is taking that stance for profit reasons. A business can simultaneously profit and operate sustainably, but it must have the appropriate priorities. The Fifth Industrial Revolution is about more efficiently using the Earth’s resources.
Human-Centered Companies Could Improve Retention Rates
Many industries are dealing with severe labor shortages. COVID-19 contributed to the problem, but it’s not the sole cause. Some long-time employees are reaching retirement age, and finding and training new workers takes time. In other cases, people look for alternatives to what they perceive as dull or physically demanding work. The challenges have prompted leaders to pursue industrial automation in earnest.
However, workers that see employers have invested in technologies that will help them may be more likely to stay for the long term. They might even recommend job openings to people they know.
The European Union-funded SHAREWORK project gives a valuable glimpse into the future. It consists of 14 hardware and software modules validated for industrial manufacturing. One of the initiative’s goals is to create a bridge between manual and fully automated tasks.
For example, one of the use cases features a robot with advanced gesture recognition technology, allowing humans to interact with it in new ways. Another advanced machine used during the project could work alongside people safely by learning their behaviors and anticipating their movements.
Better Resilience Opens More Opportunities
The European Union views Industry 5.0 as a complement to Industry 4.0. Leaders in the region have also prioritized it within their agendas because they believe resilience is essential for a stronger European economy. Some companies have already invested in technologies and methods to increase stability, such as cloud manufacturing. Seeing what happens in factories from anywhere with an internet connection lets officials be more proactive in addressing issues.
That has also occurred via the conditional monitoring of equipment. Significant downtime can cut into companies’ profits and workflows. However, a company can use advanced sensors and algorithms to turn a standard item into a smart machine. It could then learn of potential problems days or weeks before a failure occurs.
How to Implement Industry 5.0
Making a company operate with the principles of the Fifth Industrial Revolution can be complicated. Success requires identifying an organization’s current position, including its strengths, weaknesses and competitive advantages.
The European Commission also has several recommended strategies for proceeding. They all connect to the European Union’s larger goals. One option is to upskill and reskill workers, with a particular emphasis on digital skills. Digital know-how will prove exceptionally valuable as more industrial companies use technologies ranging from artificial intelligence to cloud computing in smart manufacturing operations.
Business leaders should also examine ways to become more sustainable, such as by aligning with the circular economy or determining options for using more recycled materials in products.
Data analysis can help organizations keep moving forward with Industry 5.0 initiatives. Statistics indicate advanced analytics can empower operational experts to resolve 80% of their daily queries independently. Managers with instant access to powerful dashboards and report-creation capabilities will have the data needed for quick and confident decisions.
People must emphasize research into the future, too. That might mean building executive teams tasked with exploring the potential of a next-generation technology or working on how artificial intelligence could solve a particular problem. How could it reduce injury rates throughout the workforce or improve knowledge retention during employee training sessions?
Experts also believe mass personalization will be a part of Industry 5.0. Although the Fourth Industrial Revolution began to enable it, people will likely start seeing Industry 5.0 examples of consumers buying products tailor-made for them.
In one 2022 study, UC Riverside researchers found that companies that mass-produce and customize garments can be more sustainable if customers are willing to wait for those bespoke pieces. In such a scenario, a company could uphold all three pillars of Industry 5.0 if leaders operate with care and intention.
Industry 5.0 Is the Future
Business leaders must not be too hard on themselves if they haven’t begun moving toward Industry 5.0 principles. Change takes time and effort, but it’s often worthwhile, especially when the associated advantages make companies more competitive and profitable in the modern and evolving economy.
Use this detailed overview to explore Industry 5.0 technologies and how they could impact your workforce and organization. Even if fully transitioning to the Fifth Industrial Revolution takes years, you can and should start learning practical ways to apply its pillars to your operations.
Revolutionized is reader-supported. When you buy through links on our site, we may earn an affiliate commission. Learn more here.
Author
Emily Newton
Emily Newton is a technology and industrial journalist and the Editor in Chief of Revolutionized. She manages the sites publishing schedule, SEO optimization and content strategy. Emily enjoys writing and researching articles about how technology is changing every industry. When she isn't working, Emily enjoys playing video games or curling up with a good book.