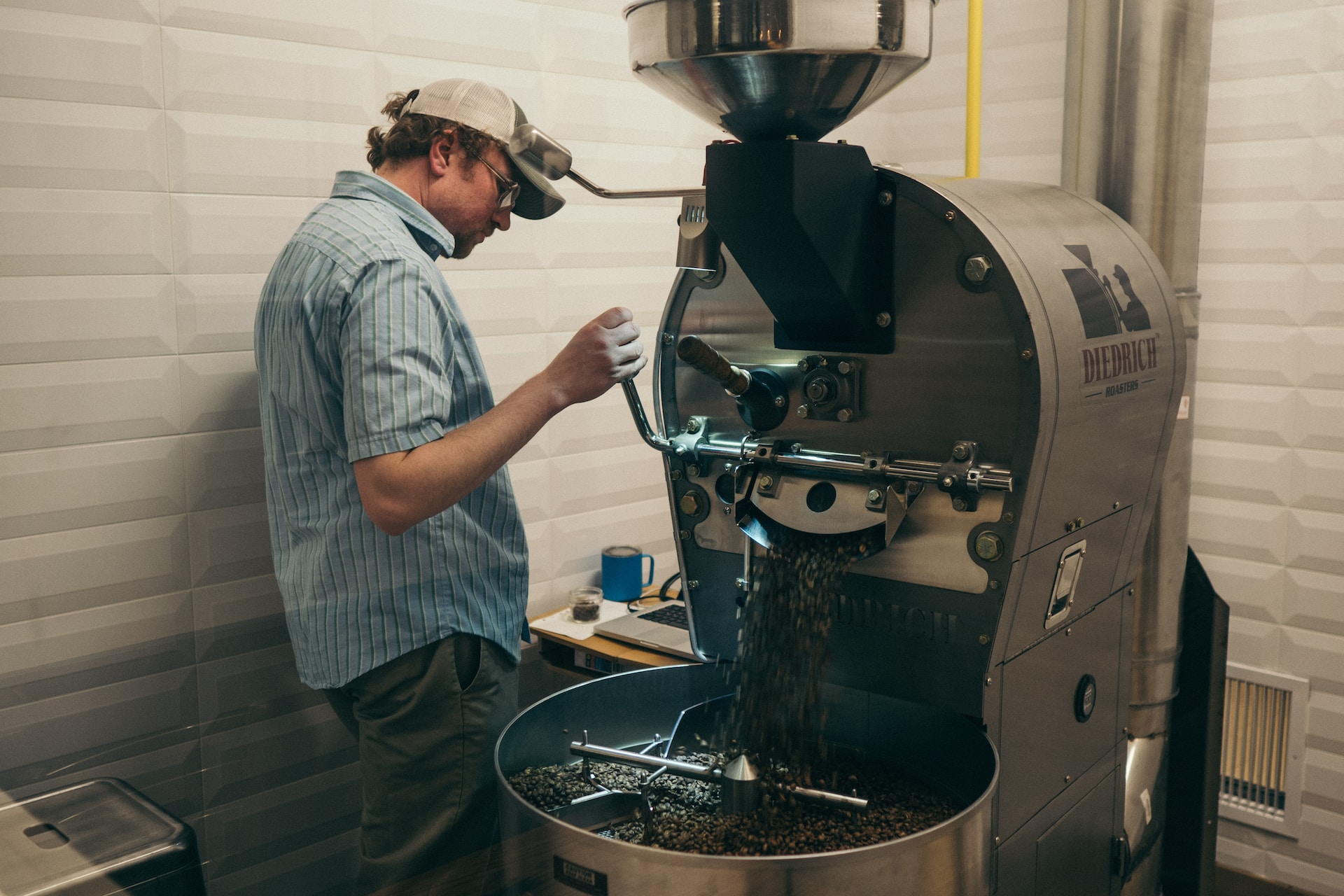
Signs a Company Needs Manufacturing Process Optimization
October 24, 2023 - Emily Newton
Revolutionized is reader-supported. When you buy through links on our site, we may earn an affiliate commission. Learn more here.
Manufacturing process optimization is increasingly important because many of today’s producers need to ramp up their operations to meet customers’ demands and stay competitive in a challenging and continually changing marketplace. Many of them pursue manufacturing process optimization to meet their goals. What are some of the main indicators they should do that, and that it’ll pay off?
High Error or Defect Rates
Company leaders should ideally track key performance indicators (KPIs) that show them whether they’re on track to meet goals or if significant room for improvement exists. A good starting point is to measure how many process errors or defects occur over a specific period. If they’re already higher than average or have trended up over time, those are strong indicators it’s time to consider manufacturing process optimization.
Dig deeper into the matter to find commonalities between what’s going wrong and why. For example, do the problems relate to a particular product or machine? Are they more frequent during a specific shift or among a given team?
After identifying those aspects, find actionable strategies to progressively address them. Lasting change won’t happen immediately, but people are more likely to stay motivated if they see the gradual, positive things happening.
It’s also useful to look for practical and accessible ways to incorporate technology into the error-reduction efforts. One recent example came when researchers designed a modular system that uses artificial intelligence and optical measurement capabilities to detect and classify errors associated with in-progress processes.
The team applied this approach to 70-centimeter-wide substrates and a roll-to-roll production process. They said one of the most advantageous things about the technology is that it classifies the detected errors. Then, people can see the information in context, using it to drive their future decisions and changes.
No matter the process changes people make, they must remember that things don’t always progress how they’d hoped. It might take longer than expected to meet a goal, or the company might seemingly reach a plateau after months of impressive progress. These things don’t mean the manufacturing process optimization has failed. However, they could indicate it’s time to tweak the current approach.
Problematic Emissions
Carbon emissions have been in the spotlight for several reasons lately. Firstly, many people are becoming more aware of the need to act now to enable a more sustainable future. They’ve realized how many production processes are extremely resource-intensive and are pushing decision-makers to start changing that. Some particularly conscious purchasers have decided they’ll only do business with companies if their representatives make ongoing progress in emissions reductions.
Regulatory pressure is another concern. Many world leaders have set ambitious net-zero emissions targets. Relatedly, some manufacturers risk steep fines if their production emissions are too high. They must take decisive, effective action and have the data proving their efforts have led to the desired results.
Manufacturing process optimization can ensure emissions stay in check. However, some company leaders need help determining the best ways to meet their goals. Manufacturers already use digital twins to test product versions before releasing them to the world. They could also rely on them in a slightly different way by letting digital twins highlight opportunities for improved processes that produce fewer emissions.
Some might also bring representatives from specialty companies in to provide further input. For example, Fero Labs is a startup focusing on reducing wastes typically seen in manufacturing processes. The company’s approach is to apply AI and machine learning to a company’s internal data, letting the algorithms find the possibilities for improvement.
The transparency of the company’s AI sets it apart by allowing users to see what the algorithms have learned, and then act upon the provided suggestions. That’s in stark contrast to how many AI tools on the market have black-box models, which give little no full information about how they reach conclusions.
Before people create plans for manufacturing process optimization, they must determine where they are now compared to their stated emissions goals. From there, they can look closer athow to close the gap and make lasting progress.
Frequent Safety Issues
International statistics indicate there are thousands of employee fatalities daily and hundreds of millions of work accidents each year. There’s no guaranteed way to prevent all of those incidents, but prioritizing safety goes a long way in reducing them. If a company has ongoing safety problems, that’s a clear indicator that things must change — and soon.
One of the more challenging parts of fixing safety-related shortcomings is that there are often multiple contributing factors to address. Perhaps an aging machine is partly to blame for several recent injuries. But it may also be true that the people using that piece of equipment never received the appropriate training.
Things also become complicated because humans become more likely to make mistakes due to aspects such as carelessness and fatigue. That means even well-trained people may end up hurt when things go wrong. Some manufacturers compensate for these realities by adding robots to the workflow. That can help, particularly since robots excel at repetitive tasks.
However, it’s also wise to talk to the employees themselves to find out more about their daily duties. Which activities feel riskiest or most difficult? Do employees have any persistent problems with the current processes? Is it easy enough for them to report safety violations they’ve noticed? Employees will provide some of the best leads on manufacturing process optimization because they engage in the daily tasks that may be more dangerous than their superiors realize.
It’s also important that workers feel invested in upholding the company’s safety culture. Staying safe is everyone’s responsibility. Highlighting that through words and actions at work is a great way to enforce and nurture an environment that supports everyone’s well-being.
Is It Time to Focus on Manufacturing Process Optimization?
These are three of the telltale signs that company leaders may need to optimize their processes to remain resilient in the marketplace. However, they’re not the only things pointing to possible problems. Manufacturing is a rapidly evolving and fast-paced industry. However, the need to value continuous improvement will remain constant.
It takes time and ongoing work to analyze current processes and find the best ways to tweak them. But staying dedicated to the task can help manufacturers boost their profits, run safer work environments and operate more sustainably.
Revolutionized is reader-supported. When you buy through links on our site, we may earn an affiliate commission. Learn more here.
Author
Emily Newton
Emily Newton is a technology and industrial journalist and the Editor in Chief of Revolutionized. She manages the sites publishing schedule, SEO optimization and content strategy. Emily enjoys writing and researching articles about how technology is changing every industry. When she isn't working, Emily enjoys playing video games or curling up with a good book.