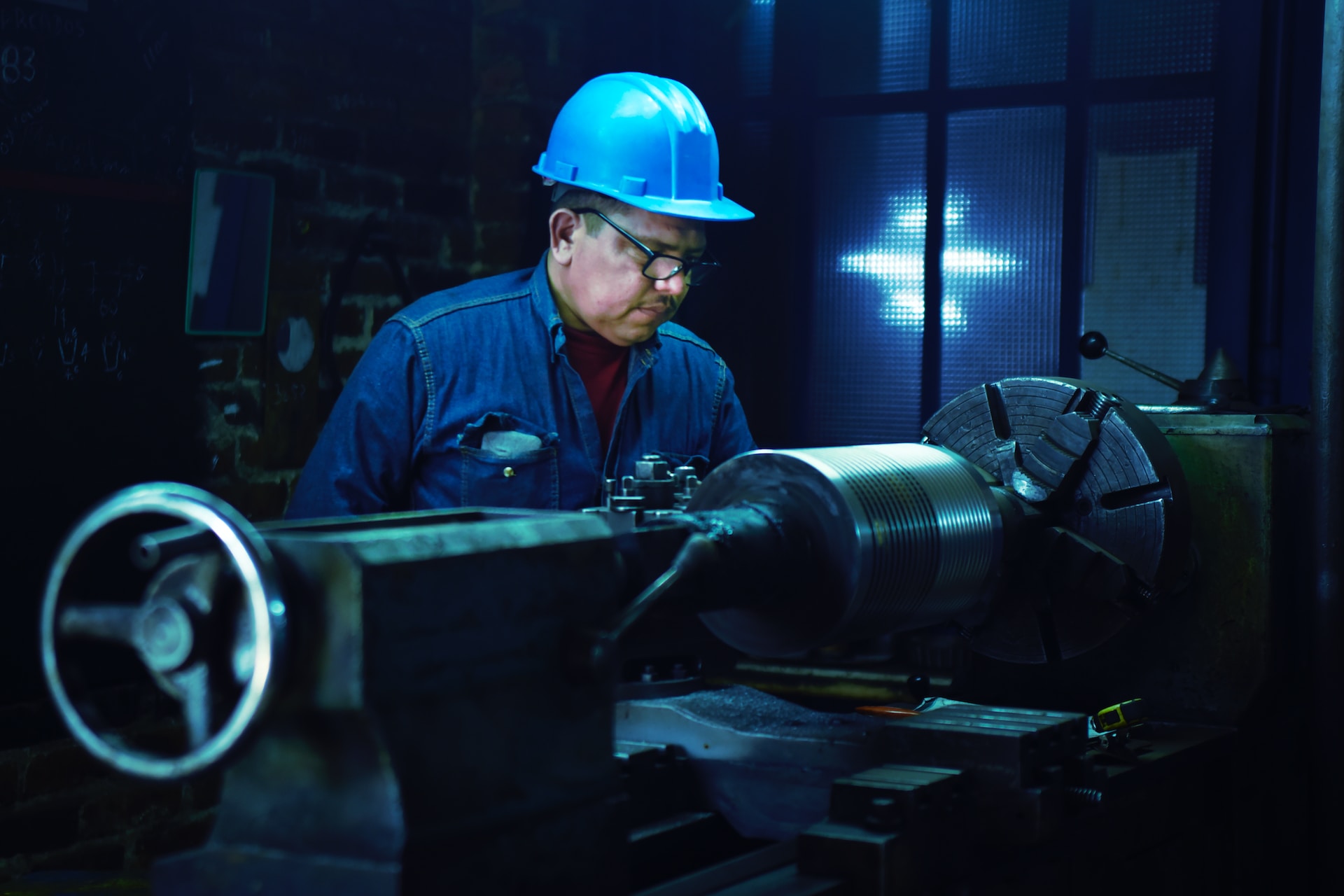
Preventive vs. Predictive vs. Condition-Based Maintenance
October 25, 2023 - Emily Newton
Revolutionized is reader-supported. When you buy through links on our site, we may earn an affiliate commission. Learn more here.
Effective maintenance is crucial to succeeding as a manufacturer, but it’s difficult to get right. Most manufacturers know not to run equipment to failure, but it’s not always clear which repair strategy is best beyond that. Some organizations prefer condition-based maintenance, others preach predictive methods and still others rely on simpler preventive measures.
The first step in choosing from these maintenance strategies is understanding the distinctions between them. To help, here’s a breakdown of each of the leading repair practices.
What Is Preventive Maintenance?
Preventive maintenance is the most common of the three major non-reactive methods. In fact, 88% of industrial facilities implement preventative measures to some extent, and it’s easy to see why. Apart from run-to-failure options, it’s the most straightforward and easy-to-implement strategy.
As the name suggests, preventive maintenance centers around ensuring equipment is in good condition before breakdowns occur. That typically involves maintaining machinery according to an OEM-recommended schedule, like drivers changing their oil every few thousand miles.
Advantages
True to its name, preventive maintenance prevents costly breakdowns, making it more cost-efficient than reactive approaches. Not requiring any additional monitoring equipment helps keep those costs low. It’s also relatively easy to practice as long as facilities keep an accurate record of each machine’s regular maintenance requirements and timelines.
Challenges
The biggest downside to preventive maintenance is that it generates considerable downtime. While it’s certainly preferable to unplanned incidents, planned repairs are a leading cause of manufacturing downtime, which leads to lost productivity. It may also result in unnecessary repairs, incurring unneeded labor and equipment costs.
What Is Condition-Based Maintenance?
Condition-based maintenance also emphasizes prevention over running to failure but takes a more situation-specific approach. Instead of maintaining equipment according to a fixed schedule, condition-based repairs respond to a machine’s real-time health factors.
This strategy often uses sensors to gather and analyze machine health data in real-time. If everything is functioning as it should, no repairs take place. If the monitoring solution detects a potential error, it alerts manufacturers so they can schedule necessary repairs.
Advantages
Like preventive strategies, condition-based maintenance minimizes the chances of an unexpected breakdown. However, only 11% of equipment failures follow an age degradation pattern, so preventative maintenance often ends in unnecessary repairs and fails to stop all breakdowns. Condition-based approaches address the other 89% and reduce repair-related downtime by using machine metrics instead of a schedule.
Challenges
While this approach is more effective at stopping breakdowns, it’s harder to implement. The necessary monitoring systems carry a high capital cost, and re-training employees can be disruptive. Responding to unexpected repair warnings can also disrupt technicians’ normal workflows, so restructuring these employees’ schedules poses a challenge.
What Is Predictive Maintenance?
Predictive maintenance takes things a step further. Like condition-based maintenance, it uses Internet of Things (IoT) sensors to monitor equipment’s real-time condition. However, instead of alerting repair technicians to current issues, it uses predictive analytics to predict when problems will happen in the future.
By analyzing early indicators of past breakdowns, the AI powering these maintenance approaches can accurately predict similar incidents before they occur. That way, manufacturers can repair machines as early as possible, achieving the preventative benefits of preventive maintenance and the low downtime of condition-based alternatives.
Advantages
Predictive maintenance minimizes planned and unplanned downtime by removing the need for unneeded repair stops and resolving issues while they’re still small. It’s also often the most accurate maintenance method, leading to longer equipment life spans and fewer breakdowns. Its reliance on the IoT and AI also makes it the most automated of the three main approaches, making up for labor shortages.
Challenges
Predictive maintenance is essentially a more technologically advanced extension of condition-based maintenance. As a result, it shares many of the same benefits and downsides but to a more extreme degree. It’s the most expensive of the three to implement, as it requires both real-time monitoring and machine learning. Developing an effective system can also be challenging, especially if manufacturers don’t have much AI programming experience.
Which Maintenance Strategy Is Best?
Preventive, predictive and condition-based maintenance all have unique strengths and weaknesses. Because every facility’s experience, resources and needs vary, there’s no one answer as to which one is the optimal maintenance strategy. Manufacturers must understand what each has to offer and determine which is the better fit for their specific needs.
Generally speaking, predictive and condition-based approaches are preferable to preventive maintenance. Roughly 30% of all preventative maintenance activities don’t add any value, and because many breakdowns don’t follow a firm timeline, this strategy fails to stop them. These simpler measures may be suitable for less critical or expensive equipment, but it’s not ideal for an entire facility.
Predictive maintenance offers the most uptime and long-term cost savings, but only in the right application. Some facilities’ predictive solutions have resulted in more downtime and no savings, thanks to high false positive rates. These systems are complex and difficult to get right, but if they’re not accurate, they can lead to excessive costs and minimal gains.
Condition-based maintenance lands in the middle in terms of cost. It’s also less likely to produce false positives than predictive measures because it relies on real-time detection, not potentially faulty predictions. While it may not offer the same savings as well–implemented predictive maintenance, it’s easier to ensure its reliability.
Given this discrepancy, predictive maintenance is best for equipment with fairly predictable wear patterns or for manufacturers with more AI experience. Condition-based repairs are a safer bet for most manufacturing applications, especially for mission-critical equipment or those with high repair costs. Some facilities may benefit from using condition-based approaches for most of their equipment but predictive maintenance for others to achieve an optimal balance.
Choosing the Right Maintenance Method Is Essential
Condition-based maintenance is an ideal repair process for many manufacturers, but not in every scenario. At times, predictive approaches offer more significant savings, and in others, the cheaper, conventional preventive method is sufficient. It all depends on the specific equipment and company at hand.
Regardless of the manufacturer in question, choosing the right maintenance method is an essential part of maximizing productivity and minimizing costs. When businesses understand where to apply each method, they can optimize their repair strategies for ongoing savings.
Revolutionized is reader-supported. When you buy through links on our site, we may earn an affiliate commission. Learn more here.
Author
Emily Newton
Emily Newton is a technology and industrial journalist and the Editor in Chief of Revolutionized. She manages the sites publishing schedule, SEO optimization and content strategy. Emily enjoys writing and researching articles about how technology is changing every industry. When she isn't working, Emily enjoys playing video games or curling up with a good book.