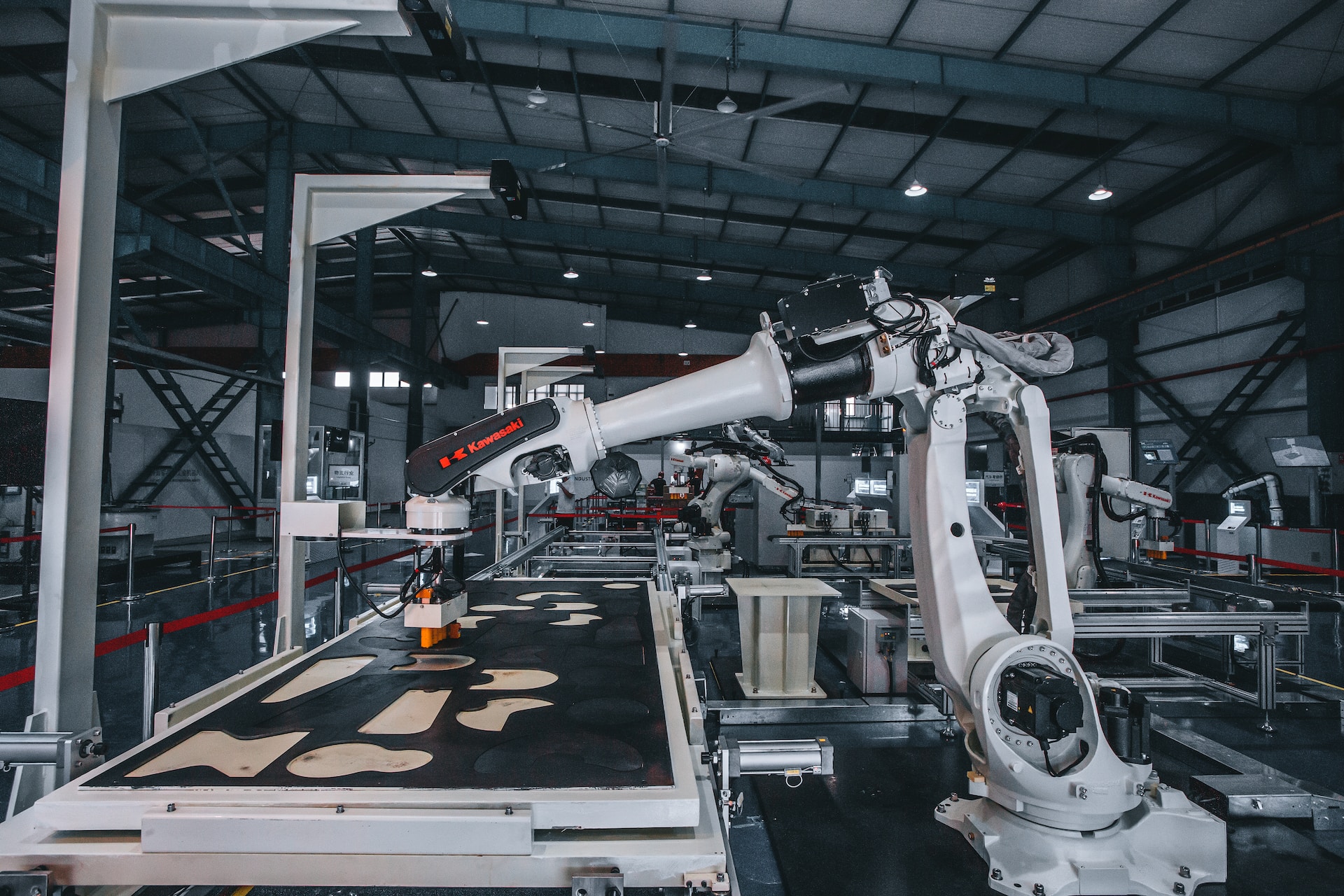
Operational Technology and Its Role in Industry 4.0
June 8, 2023 - Ellie Gabel
Revolutionized is reader-supported. When you buy through links on our site, we may earn an affiliate commission. Learn more here.
The digital revolution involves many separate technologies, so it can be hard to keep track of them all. If you’ve looked into Industry 4.0 before, you’ve likely come across the term “operational technology,” but what does this mean, and why is it important?
You’ll often see operational technology (OT) in the term “IT/OT convergence,” a core principle of digital transformation. But to understand this principle, you first need to understand what operation technology is. Here’s a closer look.
What Is Operational Technology?
Operational technology is the hardware and software that controls or monitors physical processes and environments. In a business context, OT typically refers to industrial machinery. Robots, industrial control systems (ICS) and other production equipment are all examples of this kind of technology.
These industrial machines are what most people associate with OT, but the category extends further. Any equipment that interacts with the physical world falls under this umbrella. That means vehicles, fire suppression systems, HVAC systems and even the locks on a factory door are all OT.
The National Institute of Standards and Technology (NIST) also includes devices that manage this equipment in its definition of OT. By that standard, any software or control panels you use to operate things like vehicles or robotic systems also count as operational technology.
Operational Technology vs. Information Technology
OT stands in contrast to information technology (IT). This more familiar term covers technologies that interact with digital processes and data rather than the physical world. Computers, smartphones, cloud computing services and internet resources are some of the most common examples.
There are several similarities and areas of crossover between these two categories. While IT primarily focuses on data, this data often reflects processes in the real world. Similarly, many OT devices must translate physical signals into digital data to work correctly, as they rely on digital software.
IT/OT Convergence
Despite their similarities, information and operational technology have historically been separate disciplines requiring distinct knowledge areas and skills. However, that’s starting to change with the advent of the Internet of Things (IoT). These new technologies bring IT and OT together in a practice known as IT/OT convergence.
IT/OT convergence is a defining characteristic of Industry 4.0 and refers to technologies and processes that integrate IT and OT functionality into the same system. An industrial robot with remote connectivity features is a great example. A robot like this primarily interacts with the physical world, making it OT, but it also relies on digital data and connectivity, qualifying as IT.
This convergence lets once air-gapped systems connect to and communicate with others. This shift brings the speed, insight, connectivity and data-centrism of IT to operational technologies.
Why Should Manufacturers Combine IT and OT?
Many manufacturers and other industrial businesses today are combining information and operational technology. Of course, popularity alone isn’t a sufficient reason to adopt a new technology or practice. Companies curious about IT/OT convergence should consider its following benefits.
Improved Productivity
In many cases, bringing IT features to operational technology makes them more productive. Conventional OT systems, especially automated ones, tend to struggle with flexibility. While they work quickly, they can only do so when all other factors remain consistent, causing significant delays if mistakes occur. IT/OT convergence provides a solution.
Smart robotic systems can communicate with one another, informing machines down the line about upstream disruptions. The downstream robots can then anticipate the unusual situation and adapt accordingly, maintaining efficiency despite the changing circumstances. Manufacturers can also take data from machines’ workflows to simulate changes and find new ways to optimize them.
Increased Visibility
IT/OT convergence also improves visibility. IoT connectivity lets workers see vital asset information without having to be near the asset or interrupt its workflow. On top of boosting workplace productivity, that can give manufacturers a more complete, real-time picture of their operations.
Predictive maintenance is one of the best examples of how this visibility improves operations. IoT sensors send real-time updates about machine performance, informing workers when to repair them. By getting a better understanding of each machine’s maintenance needs, manufacturers can increase uptime by 20% and extend their equipment’s life span.
Reduced Costs
As manufacturers improve their visibility and productivity through IT/OT convergence, they unlock savings opportunities. Facilities can reduce their repair spending by implementing predictive maintenance, and higher uptime will boost revenues. Similarly, using data from operational technology to create digital twins and simulate changes can reveal the best way to make them more cost-effective.
Combining IT and OT can also produce workforce-related savings. When companies approach these technologies as a single discipline, they can train and deploy one team to oversee them instead of hiring specialists with separate skill sets. As a result, businesses will use their technology and labor resources more efficiently.
Challenges in IT/OT Convergence
Blurring the lines between information and operational technology is crucial to Industry 4.0, but it involves some challenges, too. Most notably, traditional OT isn’t at risk of cybercrime, but OT with IT connectivity is. Manufacturers must be careful not to overlook this security. Because OT and IT carry unique security concerns, it may require some adaptation and increased tech spending, too.
IT/OT convergence can also be expensive and difficult to implement, given how it changes the roles many of these devices serve. Businesses must create a thorough digital transformation strategy to map out this implementation and smooth the process.
It’s also important to recognize that not every bit of operational technology will benefit the same from IT functionality. Manufacturers should identify the most disruptive use cases for their specific OT environments before investing in this shift.
Information and Operational Technology Must Work Together
When people think of digital transformation, IT devices and services tend to take center stage. Despite this preconception, operational technology plays a critical role in the shift, too. Its role changes in this transition, but it’s important not to leave it out.
IT and OT must work together for an effective Industry 4.0 strategy. Combining these technologies will take work and time, but the resulting productivity, visibility and savings are worth it.
Revolutionized is reader-supported. When you buy through links on our site, we may earn an affiliate commission. Learn more here.
Author
Ellie Gabel
Ellie Gabel is a science writer specializing in astronomy and environmental science and is the Associate Editor of Revolutionized. Ellie's love of science stems from reading Richard Dawkins books and her favorite science magazines as a child, where she fell in love with the experiments included in each edition.