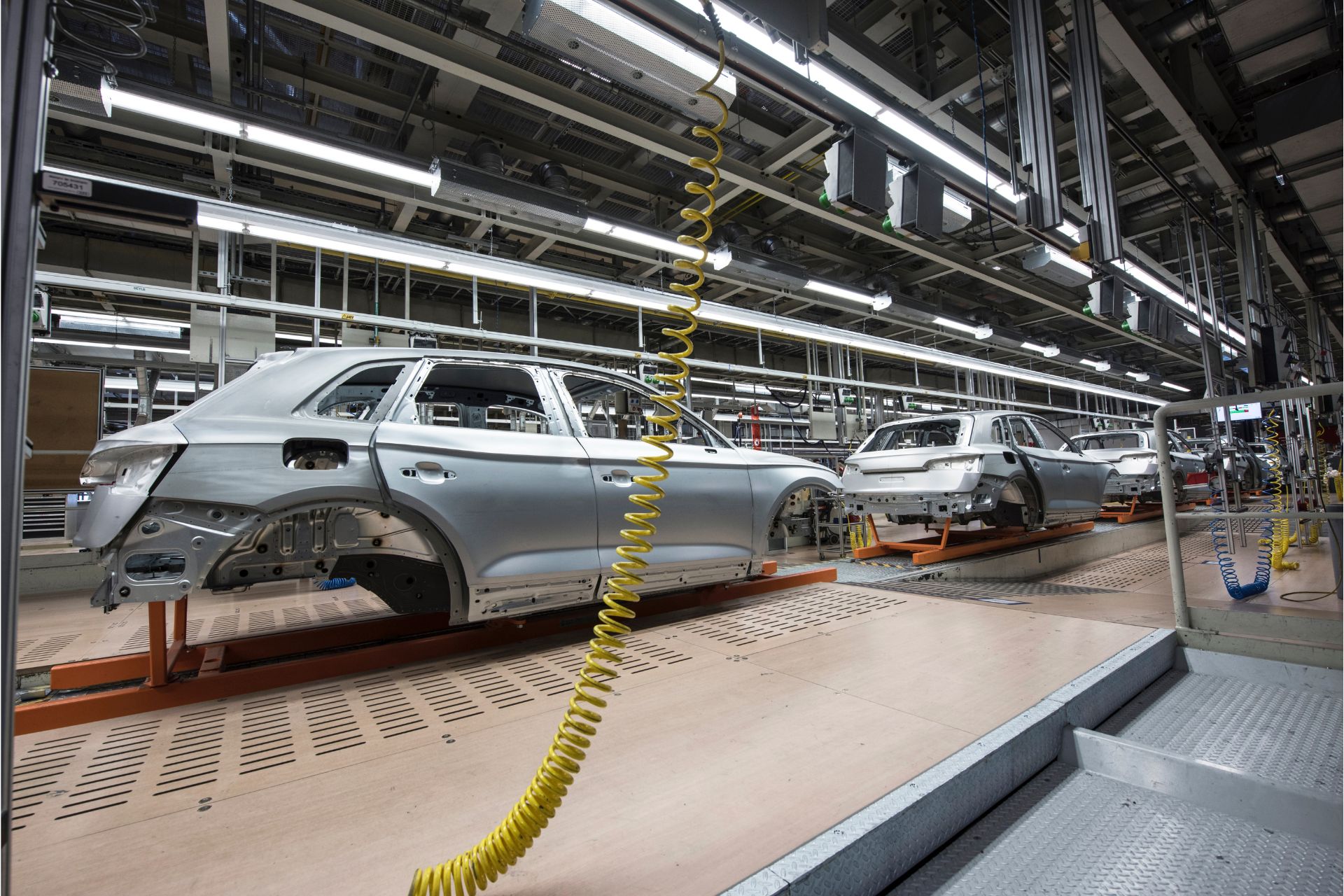
The Role of Powder Coating in Manufacturing
January 5, 2023 - Emily Newton
Revolutionized is reader-supported. When you buy through links on our site, we may earn an affiliate commission. Learn more here.
Many metal products consumers use have powder coating finishes. For example, household appliances, cars and bicycles are often coated with a powder coating and advanced military and aerospace equipment.
But how does powder coating work? How is it applied in manufacturing environments? Are there any advantages to using powder coating processes over conventional liquid paint? Learn the answers to these questions and more about its essential role in today’s modern industries.
How is Powder Coating Made?
Powder coatings add a protective or decorative finish to different surfaces, but mostly for metals. These powders consist of a few key elements, such as:
- Polymer resin systems
- Pigments
- Leveling agents
- Flow modifiers
- Other additives
The most common polymers used for these coatings are polyester, polyester-epoxy, straight epoxy, acrylics and polyurethane. These elements are then mixed in an industrial mixer, heated in an extruder, rolled flat, cooled and milled and sieved into a fine powder, similar to baking flour.
How Does Powder Coating Work?
Once the powder is ready, it’s placed into a spray gun, which applies an electrostatic charge to the particles. These particles are then attracted to a grounded metal substrate, creating a coating. This process is referred to as electrostatic spray deposition (ESD) and is often used when applying powder coatings to prevent corrosion of the product being coated.
After the ESD process, the parts enter a hot curing oven. The coating can also be cured with UV light, which is often used when applying coatings to natural wood. A chemical reaction occurs in the oven or under UV light, where the coating produces long molecular chains.
Because these chains are so resistant to breakdown, these coatings are used very often in manufacturing. It protects products that go through rough wear and tear, in addition to different types of household products.
Advantages in Manufacturing
Here are some of the advantages of using powder coating:
- Powder coatings do not contain solvents and release little to no volatile organic compounds (VOCs), making them a sustainable choice. VOCs contaminate indoor air and can cause negative health effects, including headaches and fatigue.
- Powder coatings produce thick coatings that do not sag or run, unlike conventional liquid paint, providing a stronger finish than other coatings used in manufacturing.
- Products with powder coatings cure much faster than those with liquid coatings.
- Powder-coated items usually appear to have fewer differences between horizontally coated and vertically coated surfaces than items coated with liquid paint.
- Powder-coated items can have special effects that would be impossible to achieve with liquid coatings.
- Powder-coated items typically have longer lifecycles than items with other coatings.
By understanding the advantages of powder coating, companies can decide if they want to try out these types of finishes, or stick to using traditional liquid paint for manufacturing purposes.
Disadvantages in Manufacturing
It’s important to address some of the drawbacks of these coatings, including:
- Powder-coated items can break down if exposed to UV light.
- It’s challenging to make color changes to an item once the coating is applied.
- Buying the necessary equipment (spray gun, booth, curing oven) has high upfront costs.
- Touching up defective items with these coatings can be difficult.
- Workers may have less control over the amount applied.
- It must be applied electrostatically.
- It can only be removed with labor-intensive processes.
Although powder coating applications have some disadvantages, several industries worldwide use this material to finish their products. Here are the industries that rely on powder coating most:
- Automotive
- Agriculture
- Appliances
- Lawn and garden
- Consumer products
- Electrical and HVAC products
- And more
Some companies will find liquid coatings are still more cost-effective long-term than powder coatings. It’s also possible that some manufacturers cannot perform the coating process in-house and must use a finishing service provider.
Powder Coating vs. Paint Coating?
Since its introduction in the 1940s, powder coating has become increasingly popular in various manufacturing industries. This type of coating represents around 15% of the total industrial finishing market, according to the Powder Coating Institute (PCI).
Despite the increased use of powder coating in the industrial setting, it does not mean that they are always the best for every application.
Powder coatings are the best choice if a metal object needs a durable, resistant coating. However, a conventional paint coating is just as effective for those who are trying to keep costs down and rarely coat metal products. In general, large players in manufacturing can implement powder coating processes without overspending their budgets.
The State of the Powder Coating Market
Because powder coatings offer several advantages to the average manufacturer, they’re becoming increasingly popular. One major company, PPG, recently announced that it would invest $11 million to double the capacity of its powder coating plant in Mexico. One of the main reasons for this significant investment is to meet the country’s projected future demand for these materials.
With the investment, PPG announced it would locally manufacture these innovative products:
- High Transfer Efficiency (HTE) powder coatings for difficult-to-coat surfaces
- Extreme Protection Edge powder coatings for better edge corrosion performance
- HeatSense low-temperature cure powder coating for wood substrates and metals
- Platinum powder coating for architectural aluminum extrusions
Another huge player in the industry is AkzoNobel. Its products coat some notable landmarks, including the Bird’s Nest Olympic Stadium in Beijing, the Varso Tower in Warsaw and the Hudson Yards development in New York City.
AkzoNobel also announced its CO2eRepairCalculator, a new industry-first tool to fuel body shop sustainability. This product identifies carbon levels associated with the painting and drying process on vehicles, including the amount of energy consumed. It can also provide body shops with information on the amount of VOCs emitted, helping them identify ways to improve their processes.
Powder Coating: Expect Market Growth in the Future
Powder coating has quickly become a staple across multiple industries and shows no signs of slowing down. This coating offers several advantages over traditional paint coatings, allowing manufacturers to decide which type best applies to their products.
Because companies need to apply finishes to their products for various reasons, the market will generate more revenue in the future. Powder coatings have three properties driving this market growth: cost, performance and sustainability. Expect powder coatings to become more widely used within the next few years.
Revolutionized is reader-supported. When you buy through links on our site, we may earn an affiliate commission. Learn more here.
Author
Emily Newton
Emily Newton is a technology and industrial journalist and the Editor in Chief of Revolutionized. She manages the sites publishing schedule, SEO optimization and content strategy. Emily enjoys writing and researching articles about how technology is changing every industry. When she isn't working, Emily enjoys playing video games or curling up with a good book.