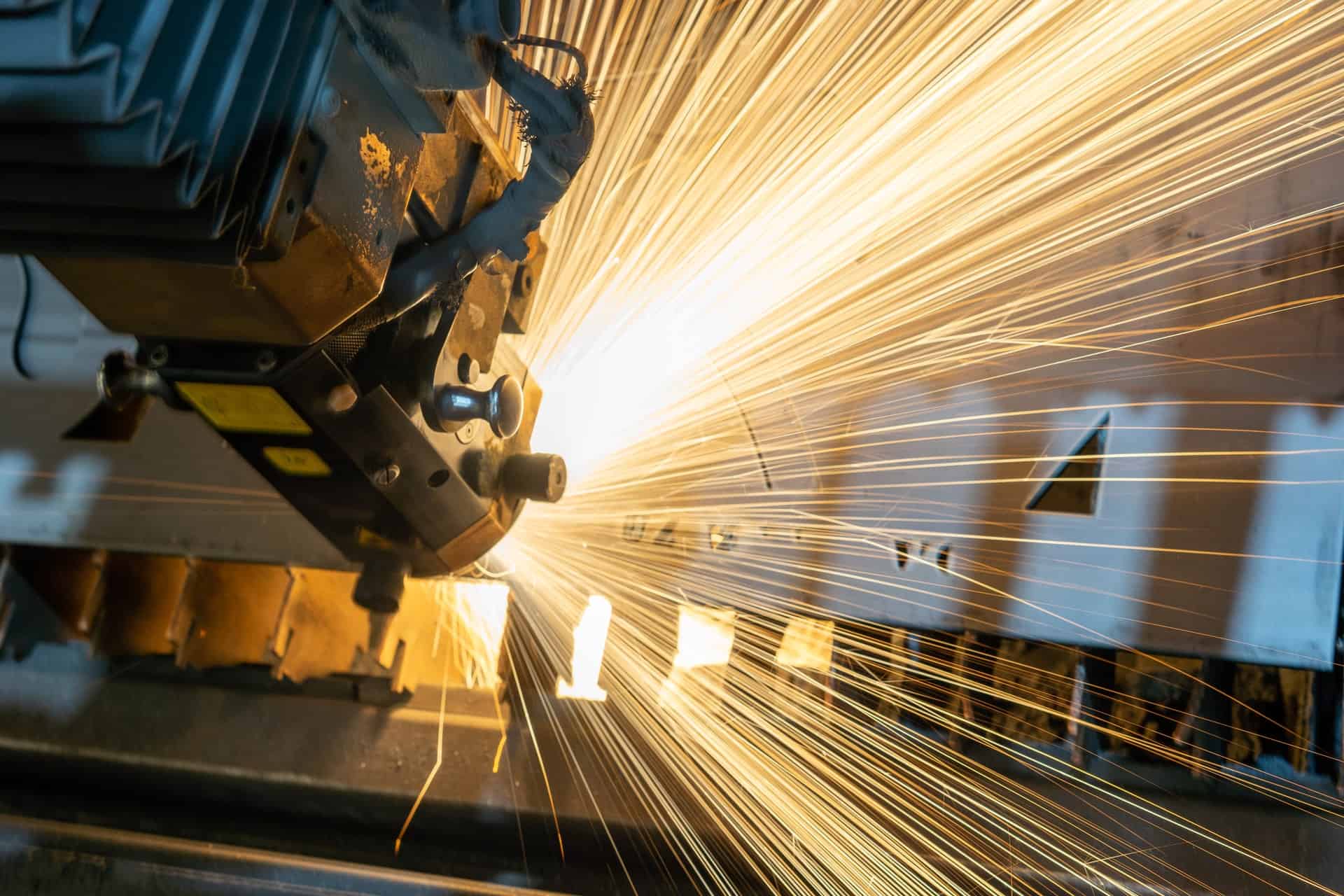
Why Does Smart Manufacturing Need to Leverage Real-Time Data?
June 15, 2021 - Emily Newton
Revolutionized is reader-supported. When you buy through links on our site, we may earn an affiliate commission. Learn more here.
Data has quickly become one of the most valuable resources that a business can have. For manufacturers, this is especially true once they’ve adopted smart technology — like IoT-powered factory sensors and smart robots. Real-time data can help owners optimize factory processes and extend the life spans of factory equipment. This is how effective data gathering and processing has rapidly become essential for modern manufacturing.
How Data Is Powering Smart Factories
In a 2015 Accenture survey of global business leaders, 84% of respondents said they expected to create new income streams with the use of industrial IoT technology. Six years on, some of these leaders have pioneered a new strategy of factory management — the “smart factory.” These factories use a range of cutting-edge technology to automate processes and streamline factory work.
This management strategy, however, is not just reliant on advanced hardware and software. It also requires a significant amount of data to be effective.
The backbone of many modern IIoT applications are smart sensors. These internet-connected devices monitor continuously for a range of data — like machine operational parameters, environmental conditions and the location of factory assets.
This real-time information can serve a wide range of applications.
Factory Applications for Real-Time Data
One common use case is predictive maintenance and analytics.
Data from real-time sensors measure machine performance parameters like timing, vibration, pressure and sound. Through the use of intelligent network switches this data is transmitted to factory management systems — like an ERP or MES — where it can be used for real-time remote monitoring purposes. This data is also sent to a database in the cloud as well.
A predictive module processes this data, using machine learning principles to “teach” an algorithm to recognize machine baselines, identify patterns and predict when a machine may be on the verge of failure.
If the algorithm, once trained, detects unusual behavior or a pattern of operating conditions that may suggest failure, it can alert factory technicians. This allows them to shut down the machine and assess the situation and perform any repairs if necessary. Some systems may also directly signal a remote control system to stop the machine, helping to prevent damage.
This is an extension of operational monitoring technology via the use of AI and big data analytics. Storing and analyzing real-time data allows a factory owner to transform a machine health tracker into a tool for predicting downtime and optimizing maintenance schedules.
The approach offers significant savings for factory owners. According to Department of Energy statistics, owners can save up to 8% to 12% over a more standard preventative maintenance plan and up to 30% to 40% over purely reactive maintenance.
Around 55% and 31% of businesses use reactive and preventative maintenance, respectively. For the majority of American factories, predictive maintenance could likely offer both a serious competitive advantage and cut down maintenance costs.
These cost savings can be extraordinarily high over a machine’s lifetime. Effective maintenance can also delay the need for replacement, helping factory owners to maximize the value of each machine they own.
Data for Smart Factory Robotics
Real-time data is also essential to many smart robotic systems. Automated mobile robots (AMRs), for example, are becoming increasingly common on warehouse and factory floors.
These robots navigate using machine vision and perform simple tasks. Navigation data comes from an on-board camera and other sensors. An AI algorithm, using a map of the factory layout, enables the robot to detect obstacles, identify navigable floorspace and navigate to its destination without interference.
Use of these robots helps factories manage a growing labor gap. Autonomous forklifts, for example, can pilot themselves through a factory, retrieve a pallet of components and deliver it to the correct workstation once it recieves the go signal.
This frees up workers for more important tasks. It also helps to cut down on the amount of strenuous or repetitive work that factory workers need to perform.
Similar technology can also be used to develop machines that are safer, even if they must operate near workers.
Cobots designed to work in close proximity with people can handle a number of common factory tasks — like sorting, packaging and machine tending — that are typically performed by employees.
Unlike conventional factory robotics, most cobots are light-weight and built for flexibility. Typically, they can be easily moved and reprogrammed for different tasks as demand shifts around the factory.
These robots come with special safety features — like padded joints and force limiters — which enable employees to work near them with less risk of injury.
Some of the most advanced cobots use machine vision, like AMRs, to analyze their work space.
These machine vision algorithms can identify workers, components and the items being worked on. Analyzing these algorithms helps to guide the cobot’s movement and reduce the risk of injuring a worker or making errors.
Efficiency and Process Optimization With Better Data
Having the right data can also make it much easier to optimize factory processes.
Many AMRs, for example, report real-time location data to factory systems as they move around the facility. This information is both useful for operational monitoring and in the long-term.
Individual data points can come together to create databases of factory traffic patterns. By analyzing this information manually or with an algorithm, managers can uncover bottlenecks or layout inefficiencys slowing traffic flow through the factory.
The same data may also reveal inefficiencies in how the factory is utilizing floor space. A heat map of traffic patterns, for example, can quickly show managers if one side of the factory tends to see more traffic than other. This suggests that they may need to redistribute resources and equipment to eliminate traffic jams.
Quality assurance operations can also benefit significantly from good data. Real-time quality assurance algorithms use information from cameras and other sensors to detect defects in finished products or components moving down the production line.
For defects that are obvious with a visual inspection — unusual marks, streaking, incorrect texture or shape — this system can help supplement or replace the labor of workers who perform visual product inspections.
An expert familar with the factory’s manufacturing and QA needs can work with an engineer to program the rules necessary to determine faulty products.
The factory can also invest in machine learning. Data from QA workers on faulty products can be used to train an AI to detect which products are defective. This allows for an automated QA system without the need for a manually-programmed algorithm.
Potential and Challenges for the Data-Driven Approach
AI and smart technology is still novel and developers of smart solutions may not always cover all the needs a manufacturer may have.
In order to collect the breadth and depth of data necessary, factory owners may also need to coordinate sensors and machines from several different manufacturers, rather than rely on a single all-in-one data and analytics solution.
Interoperability can pose a major challenge in a case like this. While increasingly important, coordinating devices from different manufacturers can be a serious technical challenge.
There are also certain risks to any AI-based approach. While often safer than conventional machines and factory systems, cobots, Aseveralomated factory technology will still pose safety risks.
Worker training needs to include information about the potential harm that these machines can cause, even with intelligent safety features. Otherwise, workers could behave in a way that puts them at risk around smart machinery.
False positives, false negatives and other unusual outputs from AI algorithms can also be hard to manage. Algorithms that are not manually programmed can sometimes be difficult or impossible to adjust. In some cases, it may be difficult to fully understand how the algorithm came to a certain conclusion.
How Manufacturers Are Using Real-Time Data in Smart Factories
The growing availability of real-time data sources has provided an invaluable asset for factory managers. Smart factory management techniques, like predictive maintenance, offer major benefits for factory owners, and as technology improves, they could become even more valuable.
Cutting-edge technology like autonomous robotics, cobots and automated management systems do have drawbacks — but the benefits they offer often outweigh these issues which is why more factories are adopting these technologies.
Revolutionized is reader-supported. When you buy through links on our site, we may earn an affiliate commission. Learn more here.
Author
Emily Newton
Emily Newton is a technology and industrial journalist and the Editor in Chief of Revolutionized. She manages the sites publishing schedule, SEO optimization and content strategy. Emily enjoys writing and researching articles about how technology is changing every industry. When she isn't working, Emily enjoys playing video games or curling up with a good book.