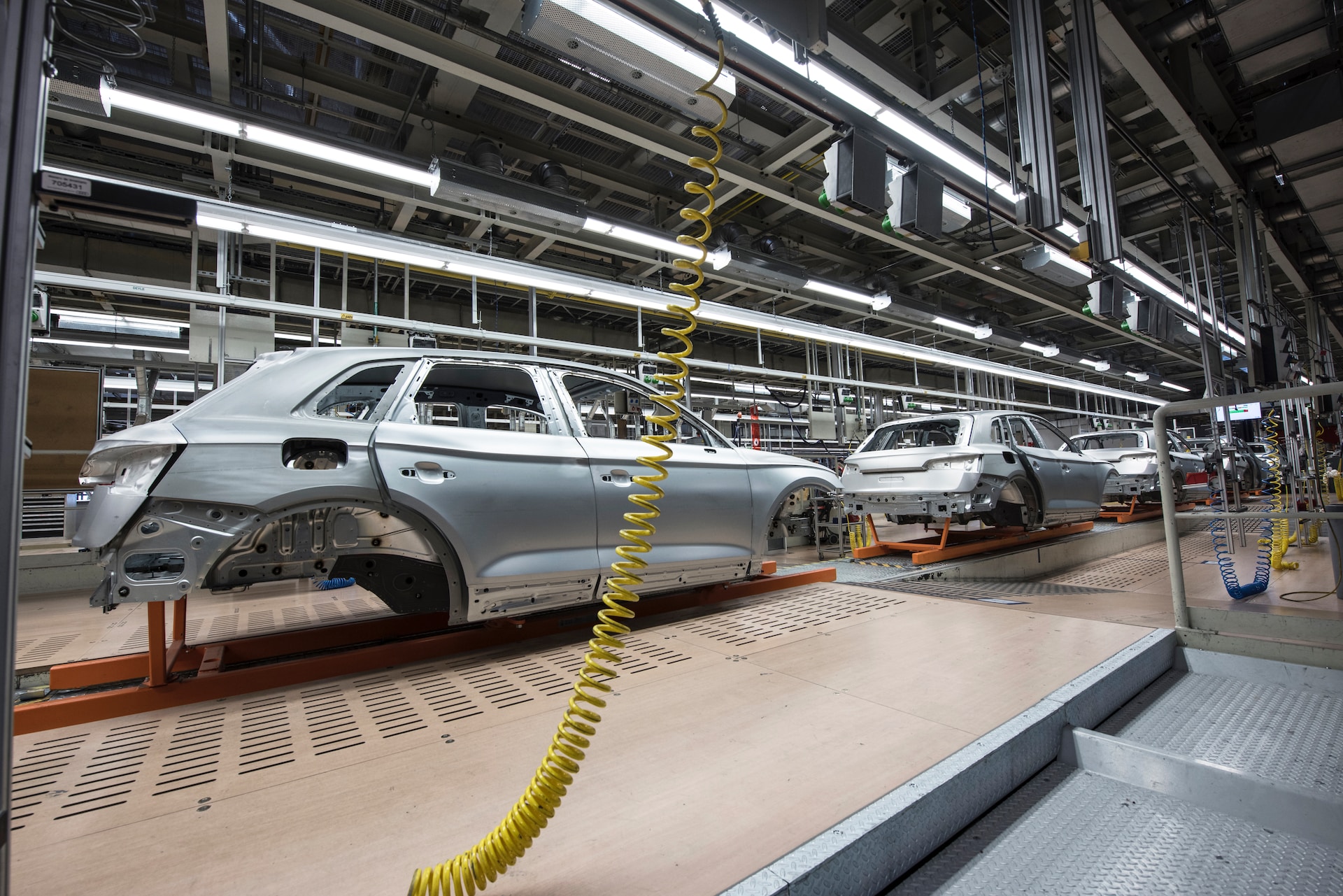
5 Steps to Reduce Downtime in Manufacturing Processes
November 9, 2023 - Emily Newton
Revolutionized is reader-supported. When you buy through links on our site, we may earn an affiliate commission. Learn more here.
Manufacturing downtime is a disruptive but all too common problem. Whether planned or unplanned, it limits throughout, increases costs and extends lead times. By the same token, when manufacturers reduce downtime, they become faster, more productive and more cost-efficient.
Just because downtime is typical in the industry doesn’t mean manufacturers should accept it. There’s almost always room for improvement and actionable steps to achieve it. Recognizing the need for downtime reduction and learning common solutions are the first steps.
Why Is It Important to Reduce Downtime?
Reducing downtime is essential because it’s both common and costly. A 2022 survey found that manufacturing plants experience 25 hours of downtime a month. That loss of productivity can cost as much as $2 million per hour in some sectors, and it’s only gotten more expensive over time.
At the same time, it can be easy to fall into the trap of assuming these losses are inevitable. After all, every business incurs some costs, no process is perfect and every machine eventually needs to stop for repairs. However, assuming that means the status quo is the best that things can be leads manufacturers to miss out on game-changing improvements.
The same 2022 study found manufacturers have room to save 1.6 million productive hours annually and boost the bottom line by 4% through a single process upgrade. Improvement is possible if manufacturers pursue it. Doing so will place them ahead of their competitors, making them more profitable and productive.
With that in mind, here are five ways to reduce downtime in manufacturing.
1. Recognize the Causes of Downtime
The first step to reducing downtime is learning what causes it. Once manufacturers identify the root causes of downtime in their facilities, they can address the disease — not the symptoms — for more effective results.
These issues may vary slightly between specific facilities, but there are a few common culprits. Some of the most significant causes of downtime include equipment maintenance, supply loss, curtailment, material issues and staffing problems. A factory may not experience all of these to extreme degrees, but chances are at least one or two of them apply.
Manufacturers should review past records to look for commonalities between downtime incidents. Some accidents may be rare, one-off problems, but any trends in this data indicate a larger, regular issue that deserves more attention. The most common shared factors are those the business should focus on most heavily.
2. Track Downtime Trends
Once manufacturers have determined their primary sources of downtime, they must track them. Just as it’s nearly impossible to effectively maximize uptime without knowing what hinders it, it’s difficult to optimize those factors without specific benchmarks. Gathering more data is the solution.
This process starts with the initial downtime source identification. Manufacturers should compile all their records on the factor in question and analyze them to calculate how much downtime it causes and the related costs. These figures will provide a benchmark against which to compare future progress against.
After setting benchmarks, manufacturers should continue to collect the same data. These records should include downtime occurrences’ duration, cost, time, operator in charge, the reason for the shutdown and any other relevant factors. It’s also best to use automated software to collect and store this information to prevent data entry errors.
3. Optimize Maintenance Practices
Maintenance is one of the most common barriers to uptime across all manufacturing sectors. Consequently, optimizing maintenance is an essential step to reduce downtime in any facility.
Repairs are such a frequent pain point because they’re necessary but most businesses rely on inefficient methods to handle them. That’s because manufacturers either run equipment to failure — which means less planned downtime but more expensive and disruptive unplanned incidents — or perform schedule-based preventive care. The latter is definitely an improvement but results in many unnecessary repairs.
In most cases, condition-based or predictive maintenance is better. Predictive maintenance reduces machine failures and repair costs by predicting breakdowns before they occur. Manufacturers then prevent the most disruptive unplanned events while only performing planned repairs when necessary for the specific machine.
4. Automate Error-Prone Processes
Human error is another frequent cause of downtime in manufacturing. Many production processes are repetitive and detail-oriented, which isn’t ideal for human workers, who will become bored or distracted. When that happens, they’ll be more likely to make mistakes. Automation is the solution.
The same workflows where humans are most likely to make mistakes are those where automation excels. Manufacturers should refer to their records to see where most production errors come from. If it falls into the heavily repetitive or physically laborious category, it’s an ideal candidate for automation.
When automating, it’s important to view it as a complement to human workers rather than a replacement. Use it to give workers more time to handle the job’s more engaging, variable sides while robots take care of the menial. Studies show this human-robot collaboration leads to higher productivity than automation alone.
5. Strengthen the Supply Chain
Another great way to reduce downtime is to prevent supply chain disruptions. Shipping delays, stock-outs and similar problems can all bring production to a halt, so a stronger supply chain will enable more uptime.
Emphasizing supply chain agility over efficiency at all costs is a good step forward. An agile supply chain can respond to incoming changes more easily, so even extreme events are minimally disruptive, preventing downtime from disruptions. Building agility requires maximizing visibility, keeping larger safety stocks and reshoring or near-shoring critical suppliers.
Regardless of the specific approach, bolstering the supply chain requires investment in smart technologies. Internet of Things (IoT) tracking solutions, cloud management platforms and artificial intelligence (AI) to make sense of the resulting data are all crucial to supply chain visibility.
Every Manufacturing Facility Should Reduce Downtime
There’s always room to reduce downtime, no matter how low it may be compared to industry averages. When manufacturers adopt this mindset, they can find new ways to cut costs and improve productivity.
Downtime may be common in the manufacturing industry, but it doesn’t have to be that way. By following these five steps, manufacturers across all sectors can maximize uptime to outpace their competition and impress their customers and downstream partners.
Revolutionized is reader-supported. When you buy through links on our site, we may earn an affiliate commission. Learn more here.
Author
Emily Newton
Emily Newton is a technology and industrial journalist and the Editor in Chief of Revolutionized. She manages the sites publishing schedule, SEO optimization and content strategy. Emily enjoys writing and researching articles about how technology is changing every industry. When she isn't working, Emily enjoys playing video games or curling up with a good book.