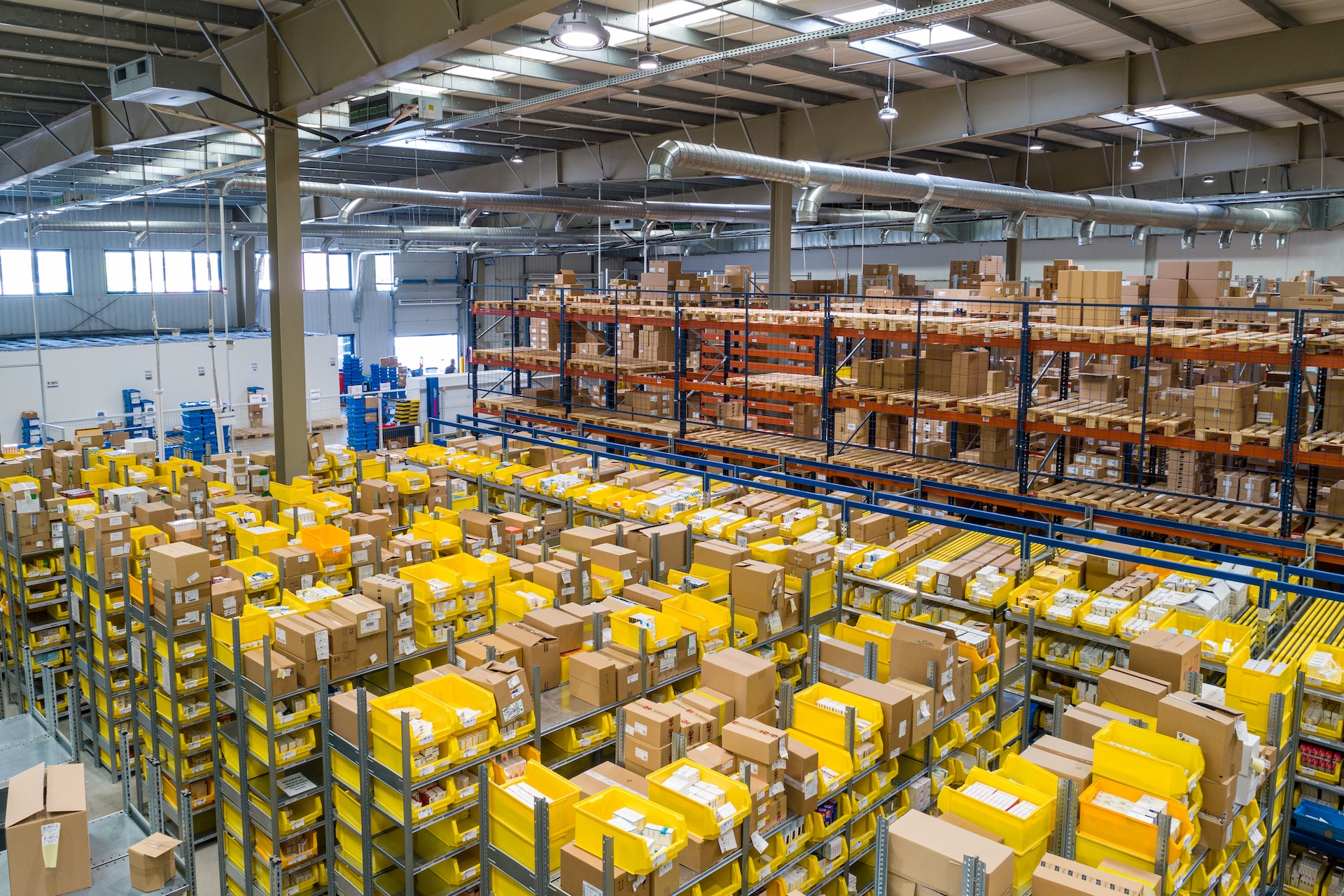
8 Warehouse Layout Optimization Tips to Boost Efficiency
September 26, 2023 - Ellie Gabel
Revolutionized is reader-supported. When you buy through links on our site, we may earn an affiliate commission. Learn more here.
E-commerce is booming, and many supply chains are grappling with disruptions and labor challenges. Amid this pressure, warehouses must become as efficient as possible. While there are many steps leading to that goal, warehouse layout optimization is one of the most important.
A warehouse’s layout impacts picking times, worker safety, automation possibilities and capacity, all of which can improve throughput and efficiency. The best possible layout is different for each facility, but here are eight ways businesses can determine theirs.
1. Identify Areas of Improvement
Warehouse layout optimization begins with understanding where the current layout is suboptimal. If the areas in most need of improvement aren’t already evident, warehouse managers should conduct assessments to reveal what needs the most attention.
The more specific these audits get, the better. General throughput figures won’t reveal much about where bottlenecks lie, but efficiency metrics from each step in the workflow will. In addition to tracking relevant KPIs, warehouse managers can also interview workers about where they feel their work slows down the most.
2. Consider Picking Techniques
Picking is one of the most common inefficiencies across warehouses. The most common picking technique is also the least efficient, so warehouses must change these workflows. Adapting layouts to accommodate faster picking methods is an important part of that shift.
Batch-order picking is often more efficient but can require more travel time for each pick. Layouts that place SKUs customers commonly order together close to one another will minimize that travel time, maximizing efficiency. Similarly, layouts enabling a linear flow of goods will better support zone picking than U-shaped warehouse flows.
Automated picking requires even more thorough consideration. Warehouse layouts must provide ample space for picking robots to move without colliding with employees or other equipment.
3. Determine the Ideal Warehouse Flow
The flow of goods is another key part of warehouse layout optimization. There are three general flow types — U-shaped, I-shaped and L-shaped — that each have unique strengths and weaknesses.
U-shaped flows are the most common and feature shipping and receiving on opposite ends of the same side of the building. It’s a good way to maximize space but is prone to congestion, especially at higher-volume warehouses. I-shaped flows follow a straight line from receiving to shipping, which is more efficient at high volumes but involves a lot of travel time.
Some warehouses may prefer an L-shaped flow. These layouts require more space but enable shorter travel times and less congestion, making them a good fit for larger facilities.
4. Highlight the Most Crucial Items
Regardless of what shape a warehouse takes, some items will inevitably be easier to pick than others. Businesses should make the most of that opportunity by placing more in-demand items in easy-to-reach locations. Doing so requires a thorough understanding of which items require the fastest lead times.
Top sellers are a natural fit for the areas closest to the loading dock, but it’s also important to consider item longevity. Between 30 and 40% of food loss occurs between production and store shelves, so warehouses in the food industry should place items with the shortest shelf life in the most accessible locations.
5. Use Technology to Your Advantage
All of these warehouse layout optimization strategies require thorough analysis and planning. That can be difficult with manual methods, but new technologies make it faster and more reliable.
Digital warehouse management systems (WMS) are one of the most important technologies to use. WMS platforms can automate inventory record-keeping and make operational data easier to see and monitor, informing more effective changes. Some warehouses have experienced 80% increases in product volume and 70% increases in inventory accuracy after using these systems.
Data from a WMS can also help create digital twins of the warehouse. These virtual models let businesses run simulations to see where bottlenecks lie and which changes would be the most helpful, taking the guesswork out of ongoing improvement.
6. Capitalize on Vertical Space
A less cutting-edge but simpler way to optimize warehouse layouts is to capitalize on vertical space. Many warehouses run out of room on the floor before realizing they have unused storage space above them. Expanding vertically before horizontally will let warehouses maximize their capacity without sacrificing room for employees to move.
Warehouses can maximize verticality in a few different ways. The most straightforward is to add additional racks on top of existing ones. The downside to this method is that it requires scissor lifts or compatible automated retrieval systems to get items from upper shelves.
Mezzanine storage is a more costly but often more helpful way to increase vertical space. Mezzanines allow workers to access higher levels safely and more efficiently and can support heavier items, but they’ll be more disruptive to install.
7. Keep Safety in Mind
Safety is another often overlooked part of warehouse layout optimization. Businesses lose an average of 11 work days per year to workplace injuries, so a safer warehouse is a fundamentally more efficient one.
When reorganizing warehouses, leave sufficient room between storage racks, especially around corners. Less space to move and a lack of visibility make collisions with forklifts or automated pickling solutions more likely. Similarly, warehouses should have sufficient lighting and minimize noise so employees can see and hear incoming hazards. Store high-volume or heavy items close to chest height to prevent unnecessary strain when picking these products.
8. Monitor Results and Be Ready to Adapt
Finally, warehouse managers should remember that they won’t likely find the best solution on the first try. They can embrace ongoing improvements by measuring relevant efficiency KPIs before and after implementing these other strategies. From there, they can review any changes to see what improved and what didn’t.
Because optimization is an ongoing process and new solutions regularly emerge, warehouses must be ready to adapt if necessary. Changing repeatedly can be challenging, but if the business and its workforce are ready for it, it’s the best way to stay as efficient as possible.
Warehouse Layout Optimization Is a Multifaceted Issue
Warehouse layout optimization is a crucial step toward becoming more efficient. While it may involve a complex set of factors, that also means there are many ways to improve it. When warehouse managers understand these strategies and possibilities, they can design the most efficient workplaces possible.
Revolutionized is reader-supported. When you buy through links on our site, we may earn an affiliate commission. Learn more here.
Author
Ellie Gabel
Ellie Gabel is a science writer specializing in astronomy and environmental science and is the Associate Editor of Revolutionized. Ellie's love of science stems from reading Richard Dawkins books and her favorite science magazines as a child, where she fell in love with the experiments included in each edition.